Wire EDM Machining Services
Obtain precision wire EDM parts with exceptional accuracy and intricacy, perfect for complex geometries requiring the highest standards. Certified to ISO 9001:2015, ISO 13485, ISO 14001:2015, and IATF 16949:2016 standards.
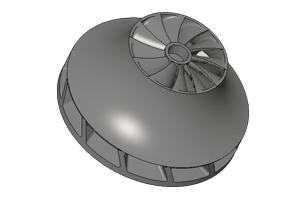
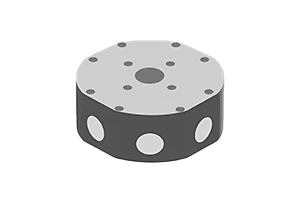
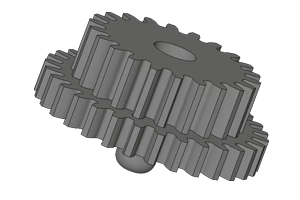
Start A Wire EDM Quote
STEP | STP | SLDPRT | IPT | PRT | SAT files
- All uploads are secure and confidential.
/01

High Quality Parts
We utilize top-tier, regularly updated EDM machinery to ensure that our clients receive workpieces machined to the highest standards of precision and accuracy, with tolerances up to +/-0.001″.
/02

Fast Lead Time
RapidTools guarantees rapid project turnarounds as fast as 1 day, maintaining high quality through an efficient wire EDM process and a dedicated team.
/03

Online Ordering and Quoting
RapidTools’s online platform provides quick quotes and real-time order tracking, streamlining projects with an efficient, transparent system for maximum convenience in the digital age.
Precision Wire EDM Machining with RapidTools
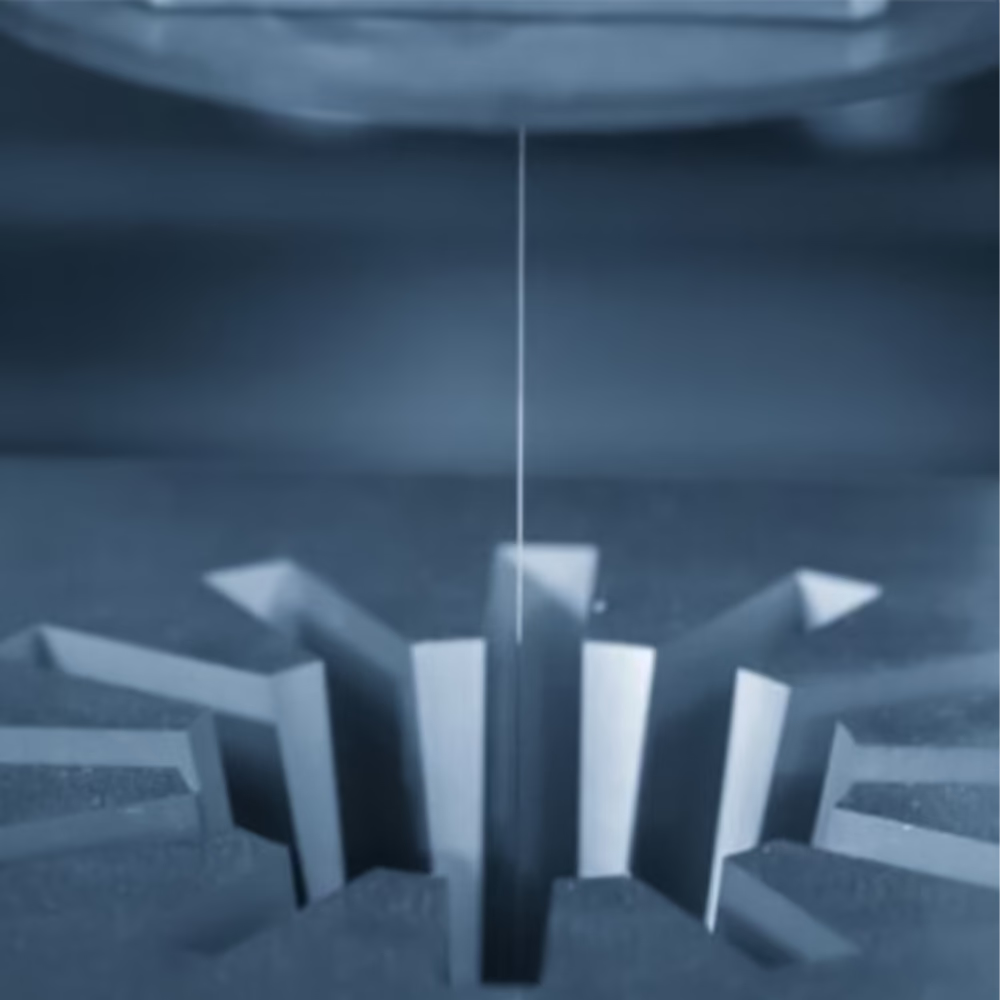
At Arapidtools, we harness the power of Wire Electrical Discharge Machining (EDM) to provide precision-engineered components to our clients. Wire EDM is a specialized machining process that uses controlled electrical sparks to shape intricate features and details in metals. This process involves creating a precise electrical discharge between two electrodes, immersed in dielectric fluid, which cuts through the metal with incredible accuracy by melting and vaporizing it.
The true strength of Wire EDM lies in its ability to machine complex contours and fine details in materials that are challenging to process with traditional CNC methods. This includes heat-treated steels, superalloys, and other specialty metals. With Wire EDM, ShengHui can achieve parts with exceptionally tight tolerances, producing features such as narrow slots and small holes with unmatched precision.
Our Wire EDM services are ideal for applications demanding the highest level of accuracy. Whether it’s producing components for aerospace, automotive, or intricate molds and dies, our technology ensures every cut is executed with the utmost precision. ShengHui’s commitment to excellence is supported by our advanced Wire EDM equipment and our team of expert technicians, making us a trusted leader in Wire EDM machining capable of delivering high-quality parts that meet the stringent requirements of any industry.
How Wire EDM Machining Works
During the wire EDM process, a metal part is submerged in dielectric fluid, and a thin wire, precisely controlled by computer systems, is fed through the workpiece. The wire, acting as both a guide and electrode, uses electrical discharges to cut the conductive material with high precision, resulting in finely finished surfaces that typically require no further processing. RapidTools’s state-of-the-art facilities ensure that even the most complex designs are executed with precision, reflecting our commitment to quality and client satisfaction.
The first step in the wire EDM process is to securely clamp the workpiece onto the machine’s worktable, ensuring it remains stationary throughout the operation. The surface is then meticulously cleaned and degreased to remove any contaminants. It’s essential that the workpiece material is conductive, as wire EDM relies on a conductive medium to function effectively.
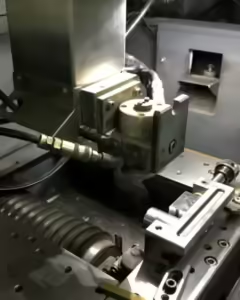
Next, a thin metal wire is fed through the machine’s guides, and both the wire and workpiece are submerged in a dielectric fluid, typically deionized water. An electrical potential is then applied, causing the fluid to break down and allowing an electrical discharge (spark) to occur, which erodes the surface of the workpiece.
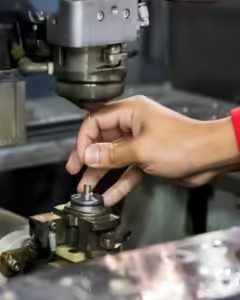
The final step in the wire EDM process involves using a computer numerical control (CNC) system to precisely guide the wire along a specific path. This allows for the accurate cutting of complex shapes and profiles in the workpiece. During cutting, dielectric fluid is continuously circulated to remove debris and maintain a stable temperature. Once the cutting is complete, the workpiece is removed, resulting in a high-quality, precisely machined part.
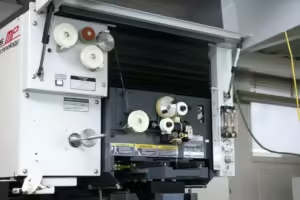
materials
Wire EDM Machining Compatible Materials
Arapidtools Wire EDM services efficiently machine a wide range of conductive materials, including tough superalloys and hardened steels, ensuring precise and durable components for demanding industries.
Metals
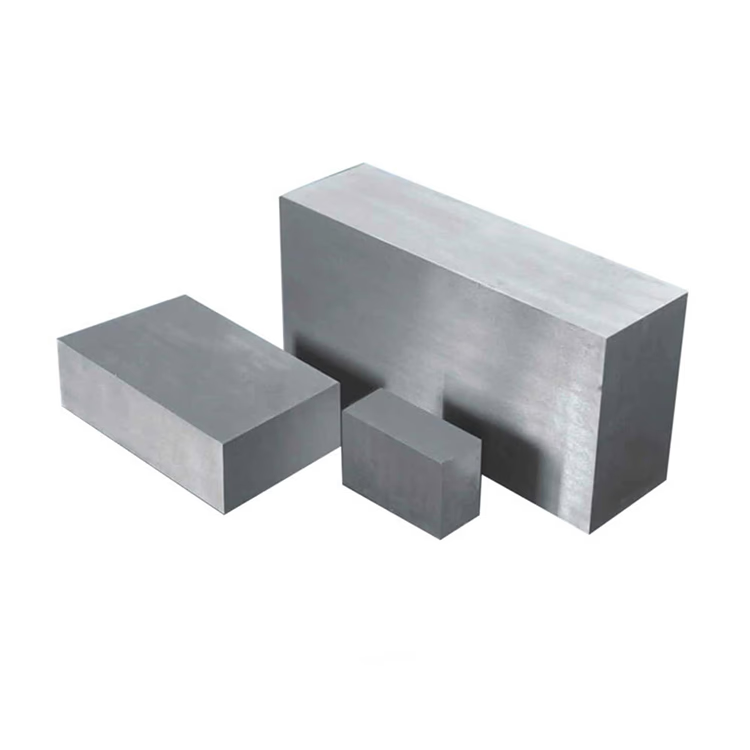
Stainless steel offers excellent corrosion resistance and strength, making it ideal for durable and long-lasting components in various industries, including medical and food processing.
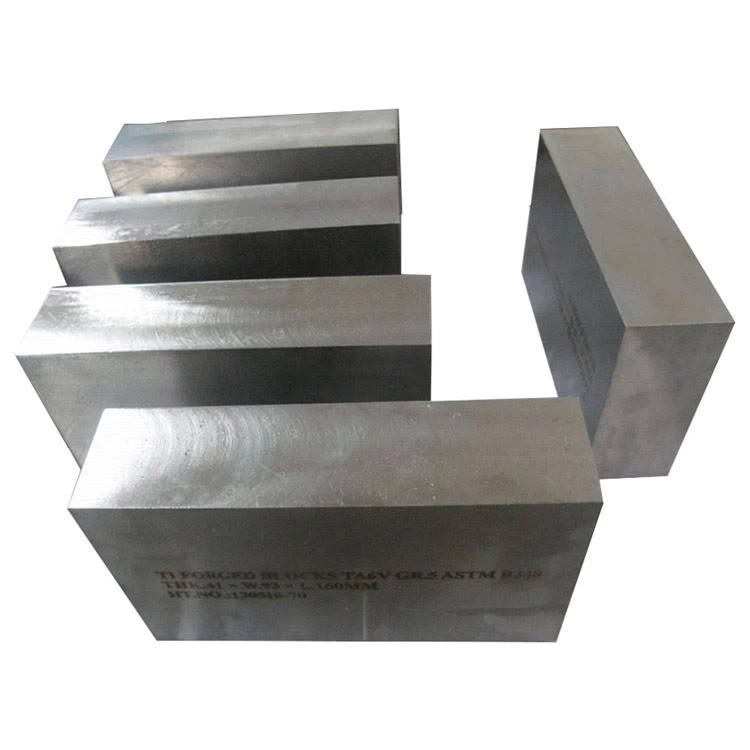
Titanium provides an exceptional strength-to-weight ratio and biocompatibility, making it perfect for aerospace applications and medical implants that require both durability and lightweight properties.
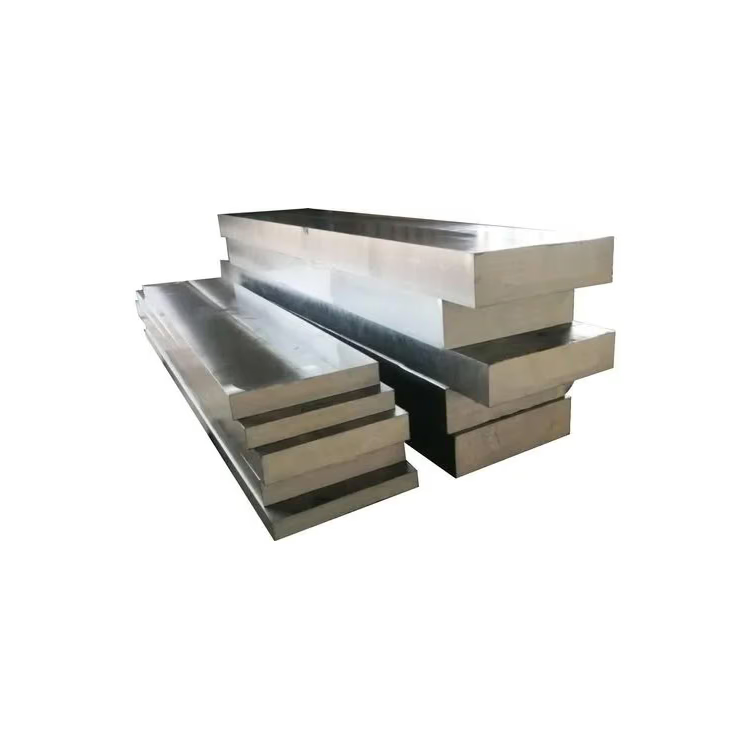
Steel and hard tool steel are known for their toughness and wear resistance, making them suitable for high-stress applications such as cutting tools, molds, and heavy-duty machinery components.
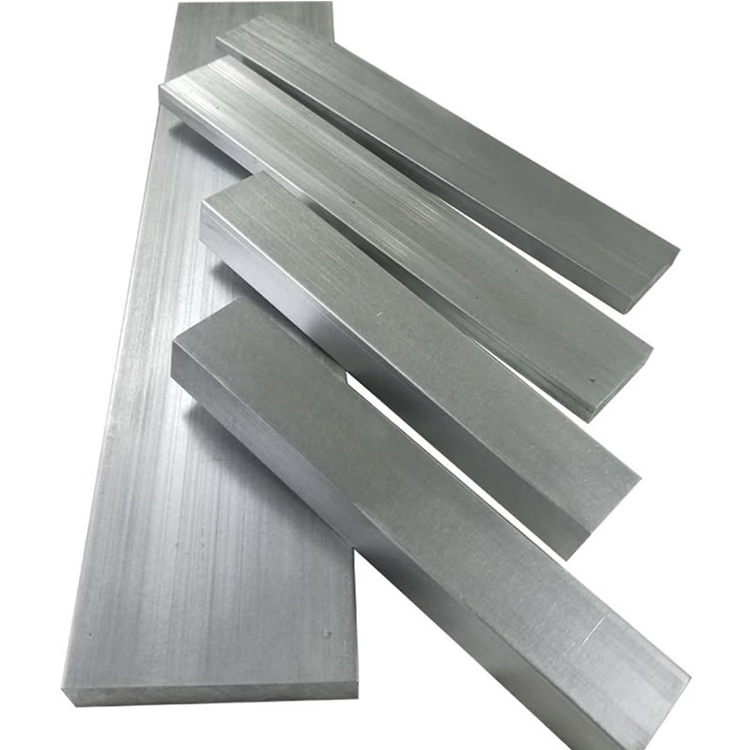
Aluminum is lightweight and highly machinable, offering good corrosion resistance and electrical conductivity. It is widely used in aerospace, automotive, and electronic applications.
Wire EDM Part Size Standards
Arapidtools can handle a wide range of part sizes with wire EDM, from intricate micro components to larger, complex assemblies, ensuring precise adherence to dimensional standards.
Small Parts (mm) | Medium Parts (mm) | Large Parts (mm) | |
---|---|---|---|
Maximum Length | 50 | 100 | 500 |
Maximum Width | 30 | 70 | 300 |
Maximum Height | 10 | 40 | 150 |
Minimum Thickness | 0.5 | 1 | 5 |
Tolerance | ±0.005 | ±0.01 | ±0.03 |
Applications of Wire Cut Parts
Wire EDM machining offers both adaptability and precision, driving innovation and quality across a range of diverse fields.
- Aerospace: It produces components with complex geometries and precise tolerances essential for high-performance demands.
- Medical Devices: It enables the manufacturing of intricate implants and surgical tools, ensuring safety and reliability.
- Tool and Die Making: Ideal for creating detailed molds, dies, and fixtures requiring exact dimensions and smooth surface finishes.
- Automotive: Facilitates the production of high-precision gears and other critical components with tight tolerances.
- Custom Manufacturing: Supports bespoke needs for specialized machinery and exotic material items.
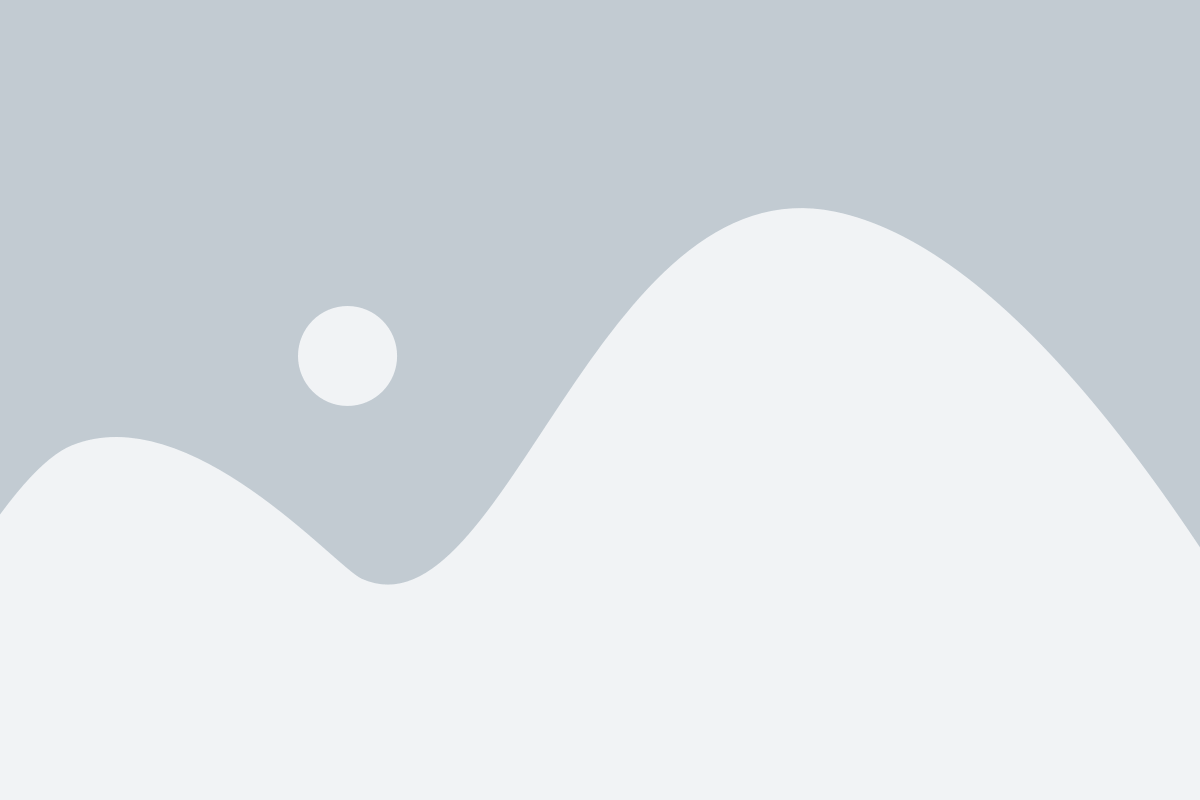
Advantages of Wire EDM Machining
Wire EDM offers several compelling advantages for precision machining:
Wire EDM offers several compelling advantages for precision machining:
- Precision and Accuracy: It is renowned for producing parts with extremely tight tolerances, often within ±0.0001 inches. This precision is critical for industries like aerospace, medical, and tool and die making.
- Complex Geometries: The method can create intricate and complex shapes, including sharp inside corners, detailed contours, and intricate patterns, which are difficult or impossible to achieve with traditional machining.
- Material Versatility: It can cut through any electrically conductive material, including hard metals like titanium and hardened tool steel, without inducing stress or distortion to the material.
- Smooth Surface Finishes: Wire EDM can achieve surface finishes as smooth as 16 microinch Ra, often requiring little to no post-machining finishing, which reduces production time and cost.
- No Contact Cutting: Since the wire never physically touches the part, there is no cutting force involved, eliminating mechanical stresses during processing. This is especially beneficial for fragile parts or those with thin walls.
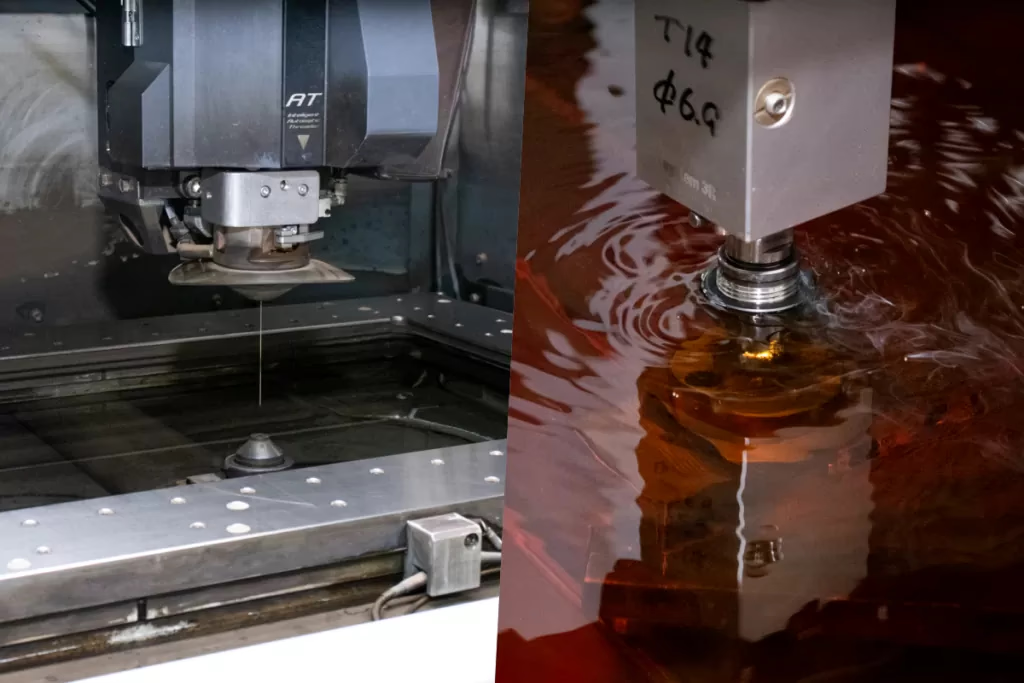
Electrical Discharge Machining FAQs
Technical FAQs
What kinds of gears can Arapidtools manufacture with electrical discharge machining?
There are two types of EDM, each with their own gear manufacturing capabilities. Wire EDM can be used to manufacture both internal and external gears, as long as there is a through hole or area for the wire to pass through. Sinker EDM can also be used to machine internal and external gears, as well as gears with more complex geometry, like helical gears.
What materials can Fictiv cut with EDM?
General FAQs
What is electrical discharge machining?
What are the types of electrical discharge machining?
What types of shapes can a wire EDM machine produce?
What happens in the EDM process?
Let's Start A New Project Today