Liquid Silicone Rubber Injection Molding Service
Manufacture custom silicone prototypes and end-use production parts in 15 days or less in a range of durometers and grades of LSR materials. Subject to availability. ShengHui doesn’t guarantee that we can provide this service at any given time.
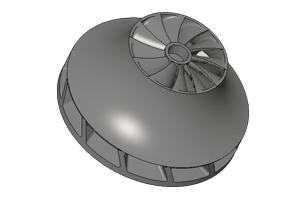
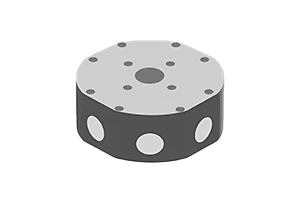
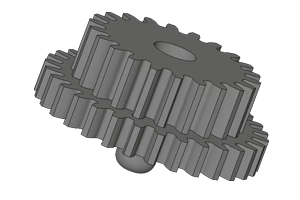
Start A New LSR Molding Quote
STEP | STP | SLDPRT | IPT | PRT | SAT files
- All uploads are secure and confidential.
What is Liquid Silicone Rubber Injection Molding
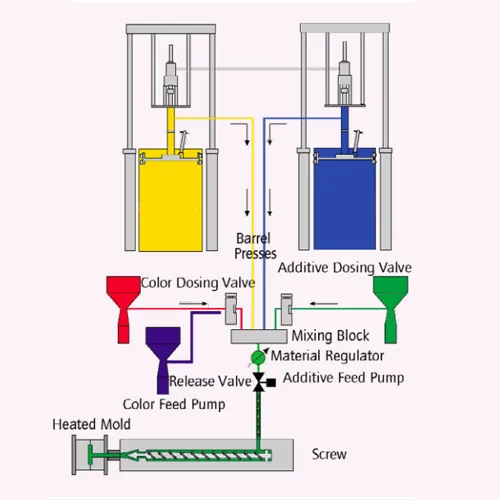
Liquid Silicone Rubber(LSR) is a two-component liquid material composed of Component A and Component B. The mixer works to thoroughly blend Component A and Component B in an exact 1:1 ratio. Additionally, for products designed in color, there is a color pump unit and a color metering section. After the thorough mixing of Component A + B, additives, colors, etc., the mixture enters the plasticizing system.
RapidTools’s Liquid Silicone Rubber Injection Molding uses these processes to ensure every component meets industrial standards.
Liquid Silicone Rubber Injection Molding Solutions
PROTOTYPING
Rapid Tooling
PRODUCTION
Production Tooling
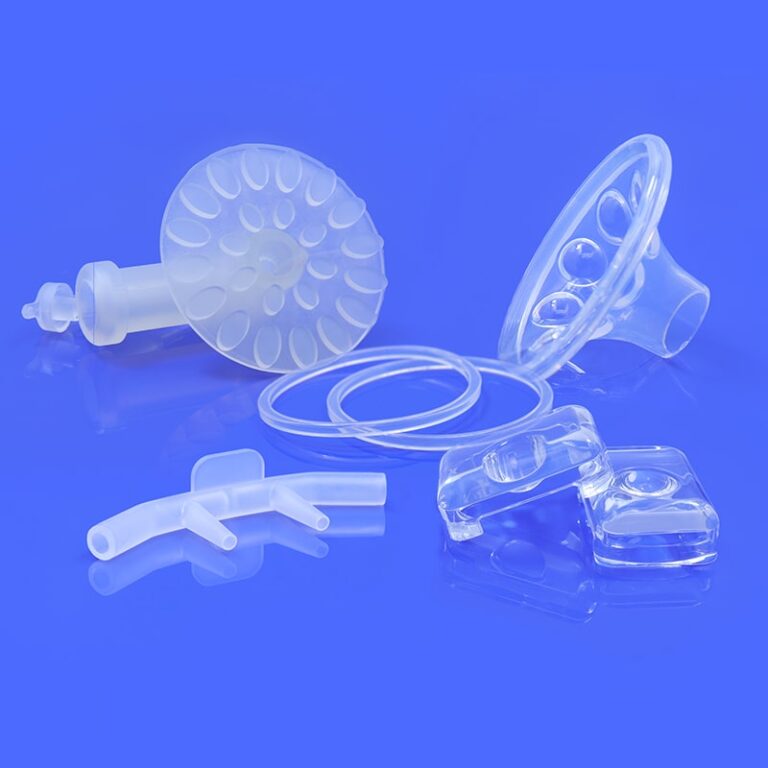
Materials for Liquid Silicone Rubber
- Standard Silicone (30, 40, 50, 60, and 70 durometers)
- Medical-Grade Silicone
- Optical-Grade Silicone
- Fluorosilicone (fuel and oil resistant)
Surface Finish Options
SPI A
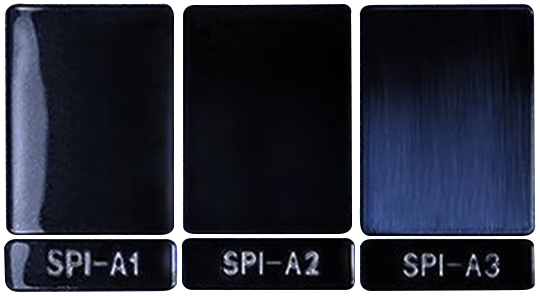
Finishing Look | High Gloss |
---|---|
SPI Finish Grades | SPI A1, A2, A3 |
Surface Roughness Ra (μm) | SPI A1: 0.012 to 0.025 SPI A2: 0.012 to 0.025 SPI A3: 0.05 to 0.10 |
SPI B
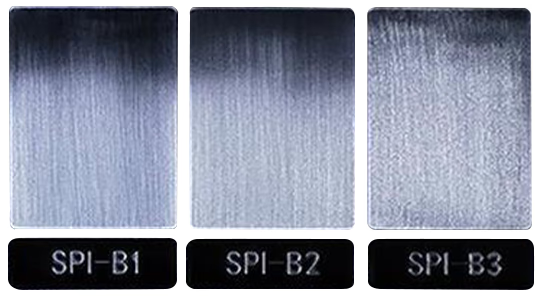
Finishing Look | Semi Gloss |
---|---|
SPI Finish Grades | SPI B1, B2, B3 |
Surface Roughness Ra (μm) | SPI B1: 0.05 to 0.10 SPI B2: 0.10 to 0.15 SPI B3: 0.28 to 0.32 |
SPI C
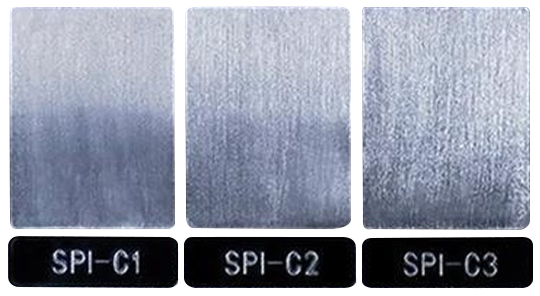
Finishing Look | Low Gloss |
---|---|
SPI Finish Grades | SPI C1, C2, C3 |
Surface Roughness Ra (μm) | SPI C1: 0.35 to 0.40 SPI C2: 0.45 to 0.55 SPI C3: 0.63 to 0.70 |
SPI D
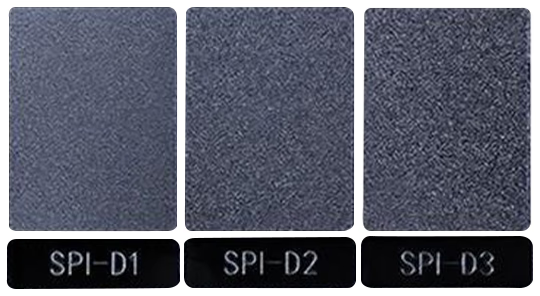
Finishing Look | Matte |
---|---|
SPI Finish Grades | SPI D1, D2, D3 |
Surface Roughness Ra (μm) | SPI D1: 0.80 to 1.00 SPI D2: 1.00 to 2.80 SPI D3: 3.20 to 18.0 |
Liquid Silicone Rubber Molding Capabilities
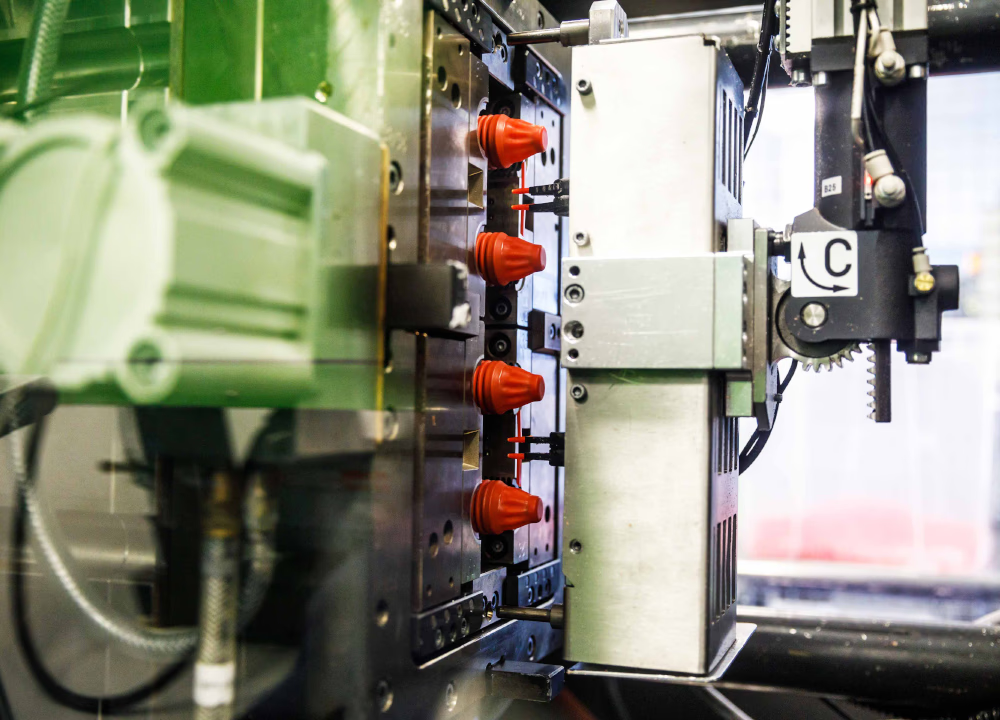
Standards | Description |
---|---|
Maximum Part Size | Up to 480 mm x 751.8 mm x 203.2 mm (Approximate) |
Minimum Part Size | As small as 2×2 mm |
Substrate Wall Thickness | From 0.5 to 3 mm, with 0.5 to 1.5 mm being ideal for flexibility and durability |
Tolerance | ±0.08 mm for critical dimensions |
Inserts | Supports metal inserts like bushings and sleeves to enhance durability and fastening |
Mold Validation | Initial sample validation (T0, T1, T2) provided before mass production |
Inspection and Certification Options | First Article Inspection, ISO 9001 (Quality), ISO 13485 (Medical) |
Lead Time | Typically 15 to 45 business days, depending on complexity |
How Does Liquid Silicone Rubber Molding Work?
Due to the flexible nature of LSR, parts are manually removed from the mold, and thus, ejector pins are not built into the mold design. Like a standard aluminum tool, an LSR molding tool is fabricated using CNC machining to create a high-temperature tool built to withstand the LSR molding process. After milling, the tool is polished by hand to customer specifications, which allows six standard surface finish options.
The finished tool is loaded into an advanced LSR-specific injection molding press that is precision geared for accurate control of shot size to produce the most consistent LSR parts. Since LSR is a thermosetting polymer, its molded state is permanent—once it is set, it can’t be melted again like a thermoplastic. When the run is complete, parts (or the initial sample run) are boxed and shipped shortly thereafter.
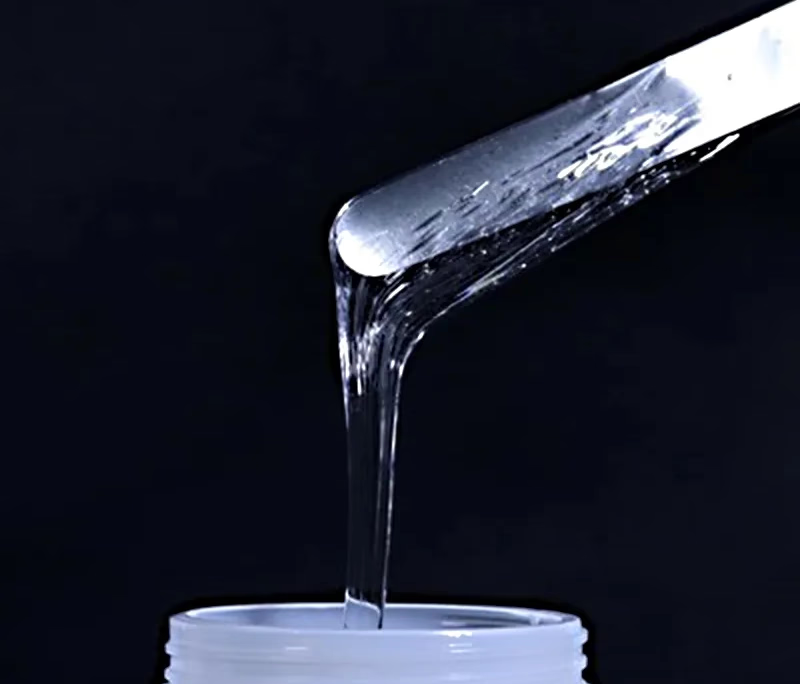
Advantages of Liquid Silicone Rubber
Liquid Silicone Rubber molding can reduce assembly and labor costs, enhance part strength and reliability, and allow for the integration of multiple materials and complex components.
- Complex Geometries: LSR molding can produce intricate and detailed parts with high precision.
- Elasticity: LSR parts are highly flexible and can withstand stretching and deformation.
- Heat Resistance: LSR can operate effectively in high-temperature environments without losing its properties. Fast Cycle Times: The injection molding process is efficient, allowing for high production rates.
- Smooth Surfaces: Parts produced have a smooth, high-quality surface finish.
- Medical Applications: LSR is biocompatible, making it suitable for medical devices and healthcare products.
- Customizable Properties: LSR can be engineered to meet specific requirements, including hardness, color, and other properties.
- Non-Toxic: LSR is generally non-toxic and environmentally friendly, contributing to sustainable manufacturing practices.
Applications of Liquid Silicone Rubber
RapidTools’s liquid injection molding cells produce durable LSR and LSR 2k parts for various industries:
- Automotive: Custom LSR components like connector seals, sensor parts, key fob membranes, vibration cushions, and HVAC system seals.
- Life Sciences: High-volume seals, gaskets, valves, and diaphragms for medical devices, drug delivery components, and wearable healthcare monitors.
- Industrial: LSR membranes and diaphragms in gas heaters, and seals for safety products like smoke detectors.
- Consumer Products: LSR parts in kitchen, bathroom, and personal hygiene products, as well as audio devices like headphones and speakers.