Insert Molding Service
Custom insert molding services for high-quality prototypes and on-demand parts are available at RapidDirect. Get online quotes at competitive prices with short lead times. With rapid tooling production as fast as 2 weeks, you can quickly move from design to production.
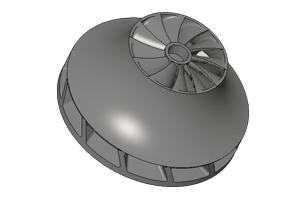
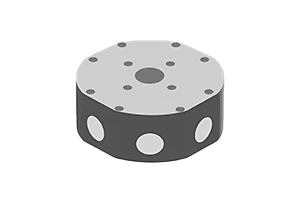
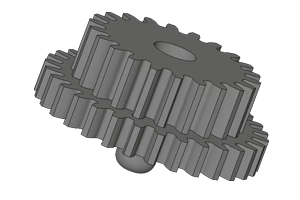
Start A New Insert Molding Quote
STEP | STP | SLDPRT | IPT | PRT | SAT files
- All uploads are secure and confidential.
What is Insert Molding?
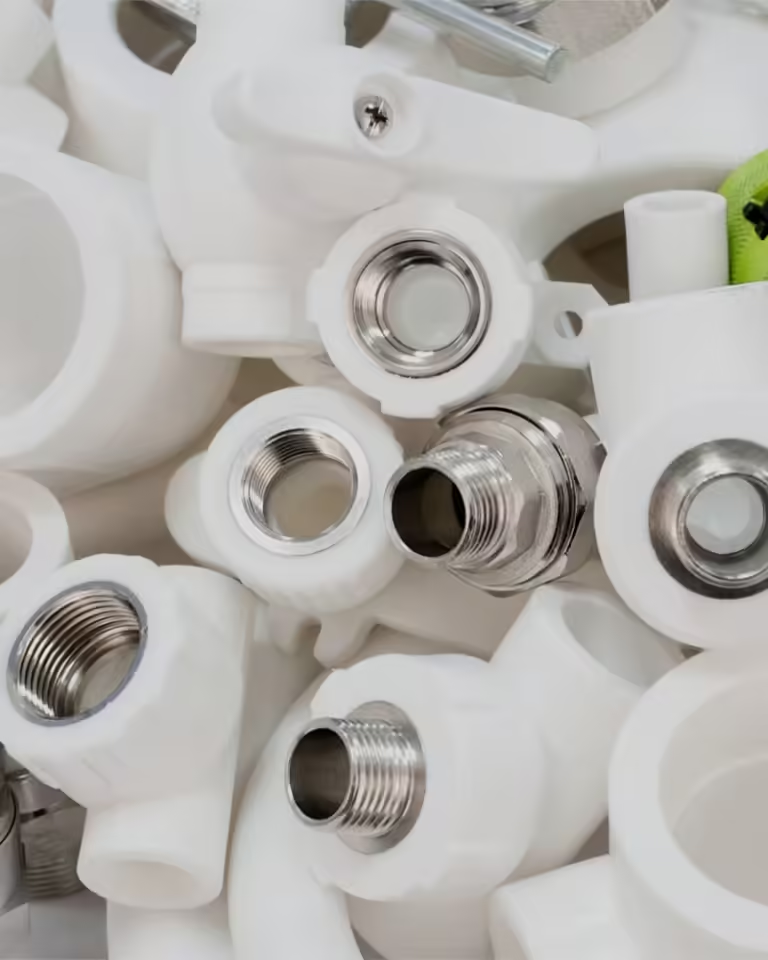
Insert molding is an injection molding technique where a plastic or metal insert is placed into a mold cavity before injecting plastic material around it. This process creates a strong, durable part with a solid bond between the insert and the molded plastic. RapidDirect’s insert molding services ensure high-quality, robust parts with permanent integration of inserts into the plastic.
Insert Molding Tooling Solutions
PROTOTYPING
Rapid Tooling
Quickly receive design feedback and validation with top-quality prototype tooling. Produce small batches of plastic molded parts with precise injection molding prototypes. We specialize in creating prototype molds within days, allowing you to conduct functional tests and gauge market interest efficiently.We implement affordable aluminum tooling to help you reduce financial risks before full-scale production.
PRODUCTION
Production Tooling
materials
Materials for Overmolding
We provide a wide selection of thermoplastic and thermoset materials, carefully chosen for their specific performance characteristics to suit various applications.
Plastics

ABS is strong, durable, and offers good resistance to heat and impact. It’s preferred for automotive components and consumer goods.
- ABS Beige(Natural)
- ABS Black
- ABS Black Antistatic
- ABS Milky White
- ABS+PC Black
- ABS+PC White
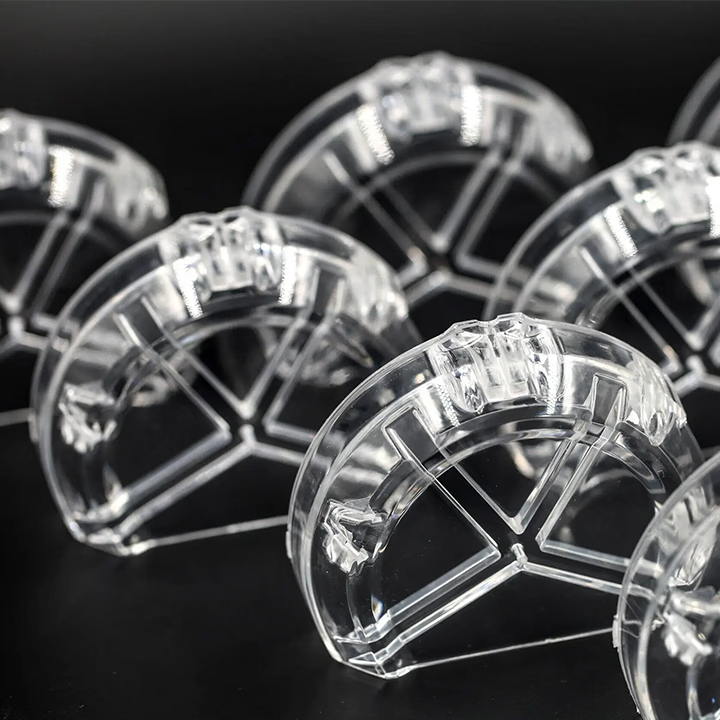
Polycarbonate is extremely durable and has high impact resistance, along with excellent clarity, used for bullet-proof glass and protective gear.
- PC Black
- PC Transparent
- PC White
- PC Yellowish White
- PC+GF30 Black
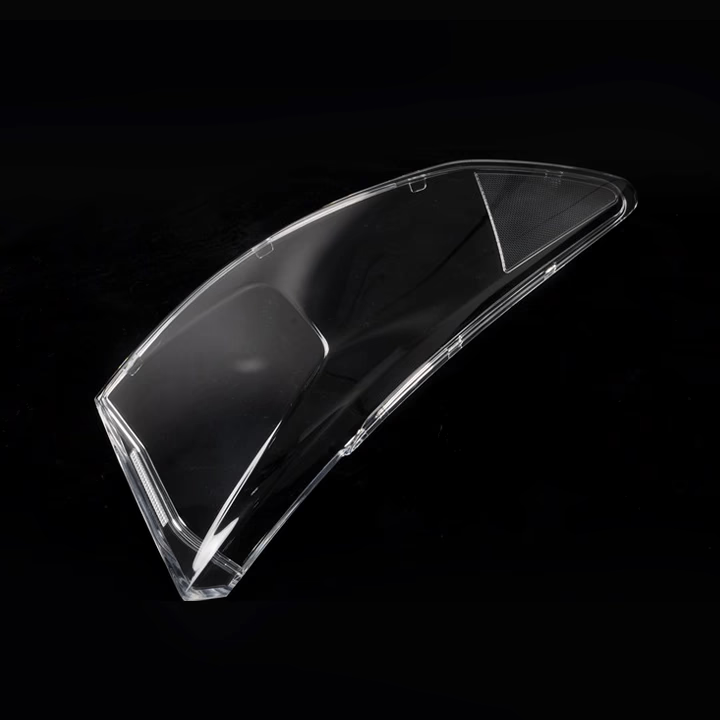
PMMA, or acrylic, is known for its crystal clarity and weather resistance, making it ideal for outdoor fixtures and display cases.
- PMMA Black
- PMMA Transparent
- PMMA White
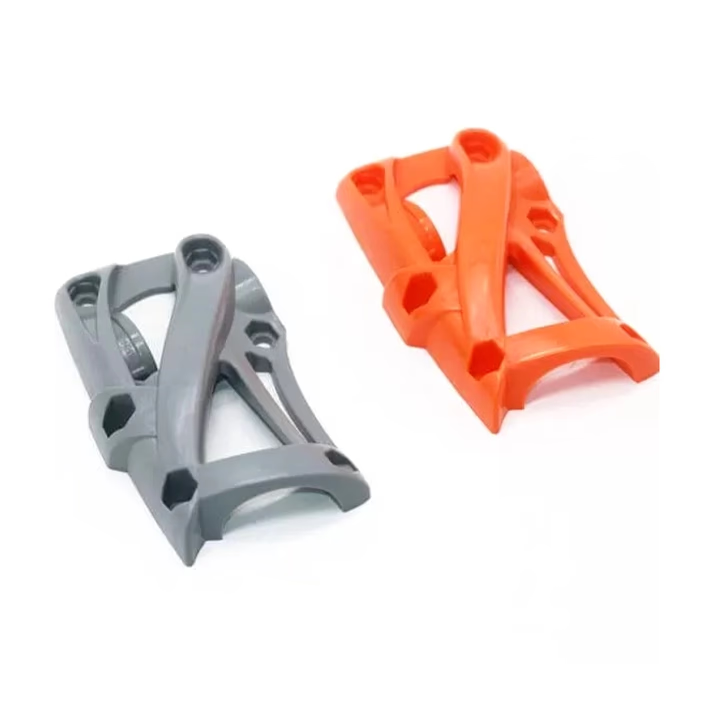
POM is strong, with a low friction surface and good dimensional stability, perfect for precision parts in mechanical applications.
- Dark brown (coffee) POM 100AF
- POM Black
- POM Blue
- POM White
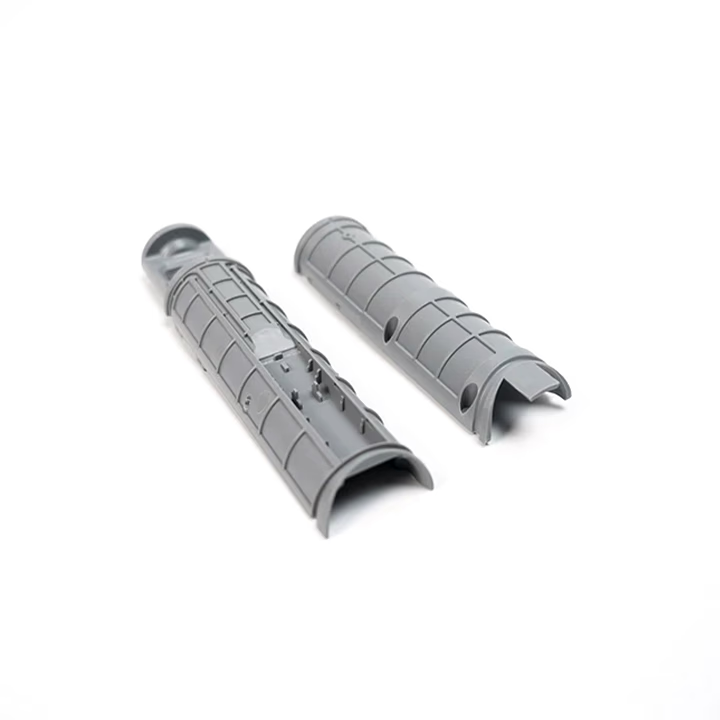
Nylon is versatile, strong, and wears well against friction, commonly used for gears, bearings, and other wear-resistant surfaces.
- PA(Nylon) Blue
- PA6 (Nylon)+GF15 Black
- PA6 (Nylon)+GF30 Black
- PA66 (Nylon) Beige(Natural)
- PA66 (Nylon) Black
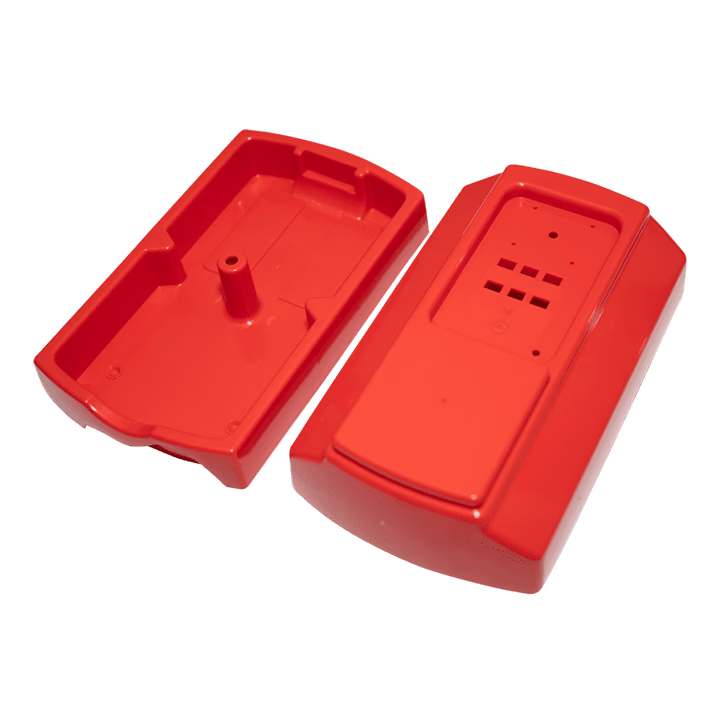
Polyethylene is lightweight and has high resistance to impact, widely used in packaging and containers.
- PE Black
- PE White
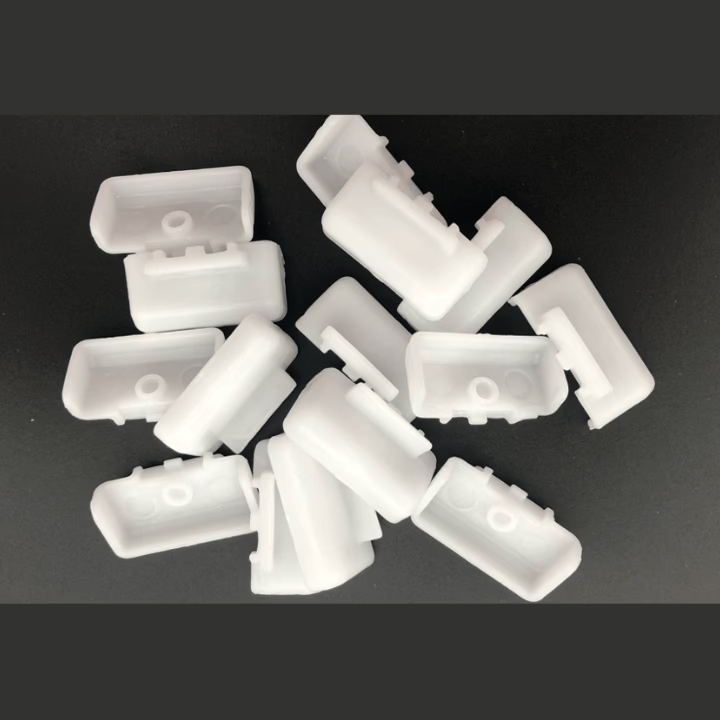
PEEK is renowned for its high temperature resistance and strength, often used in aerospace and medical implant manufacturing.
- PEEK Beige(Natural)
- PEEK Black
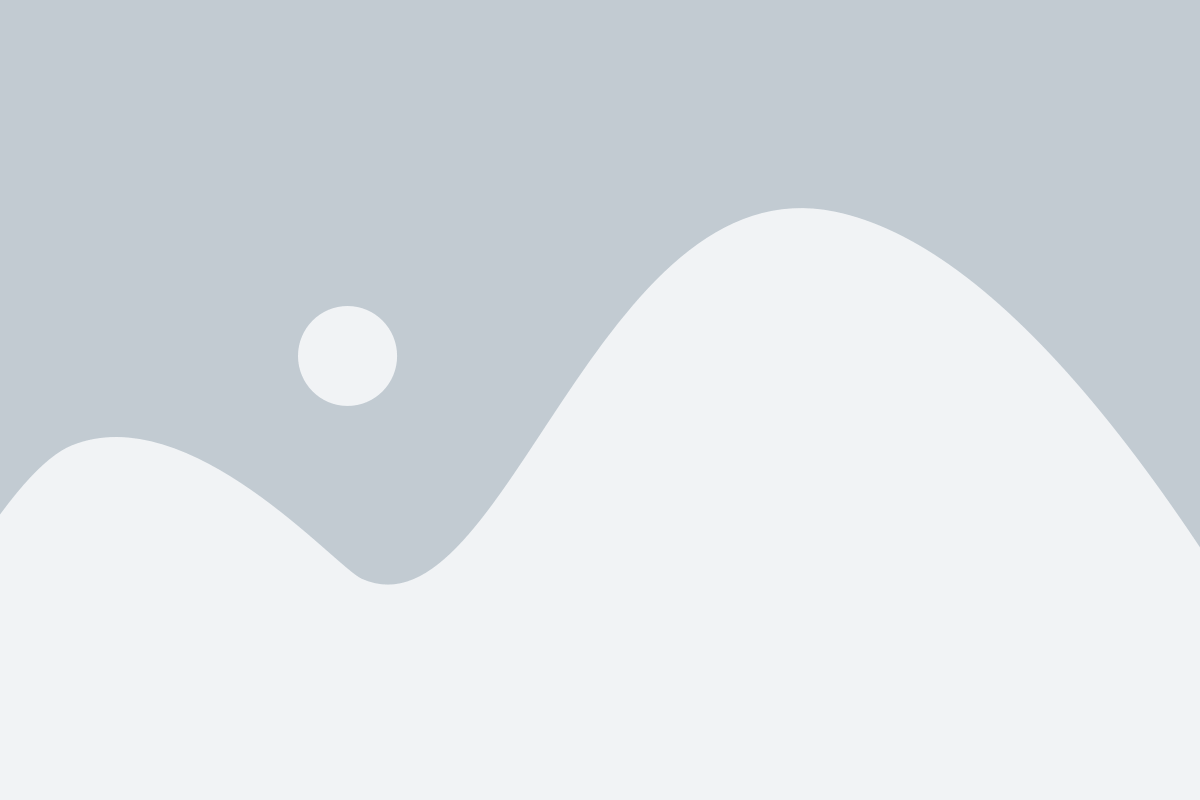
Polypropylene is tough, has excellent chemical resistance, and is used for automotive parts, containers, and in packaging.
- PP Black
- PP White
- PP+GF30 Black
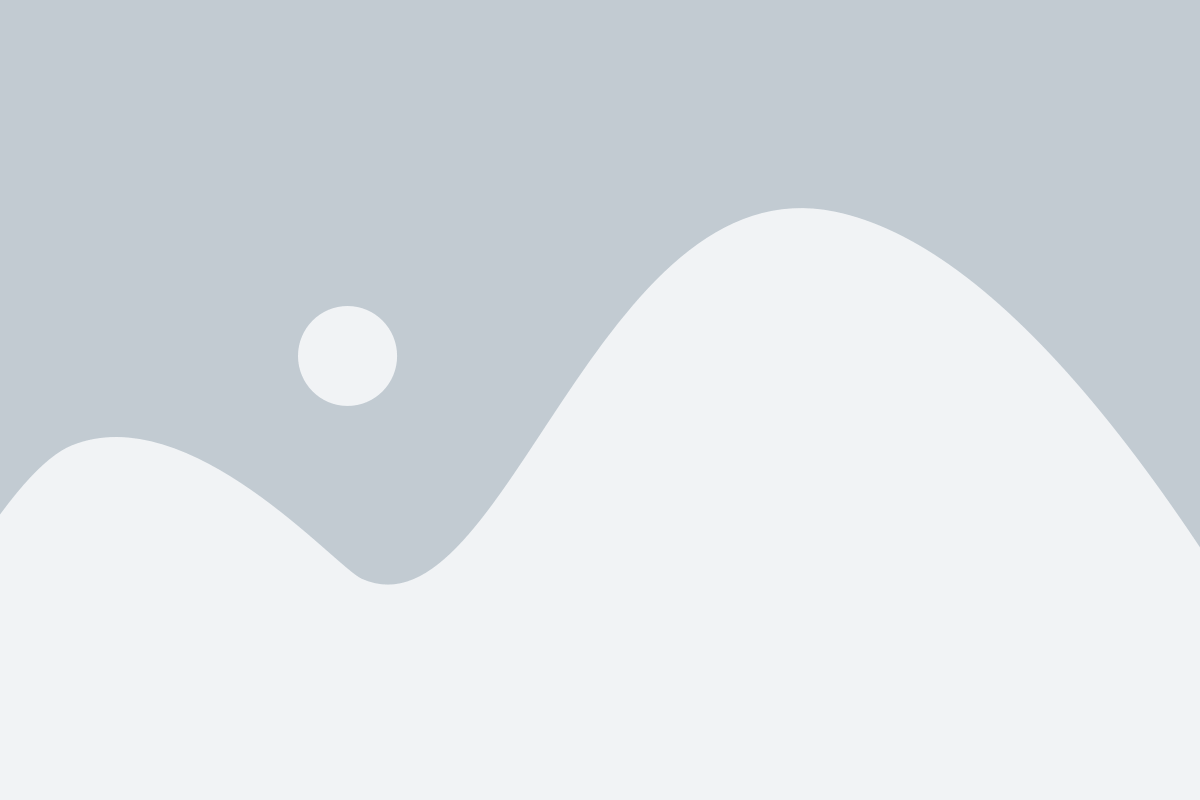
HDPE is known for its high strength-to-density ratio, resistance to impacts, and is used in making bottles and corrosion-resistant piping.
- HDPE Black
- HDPE White
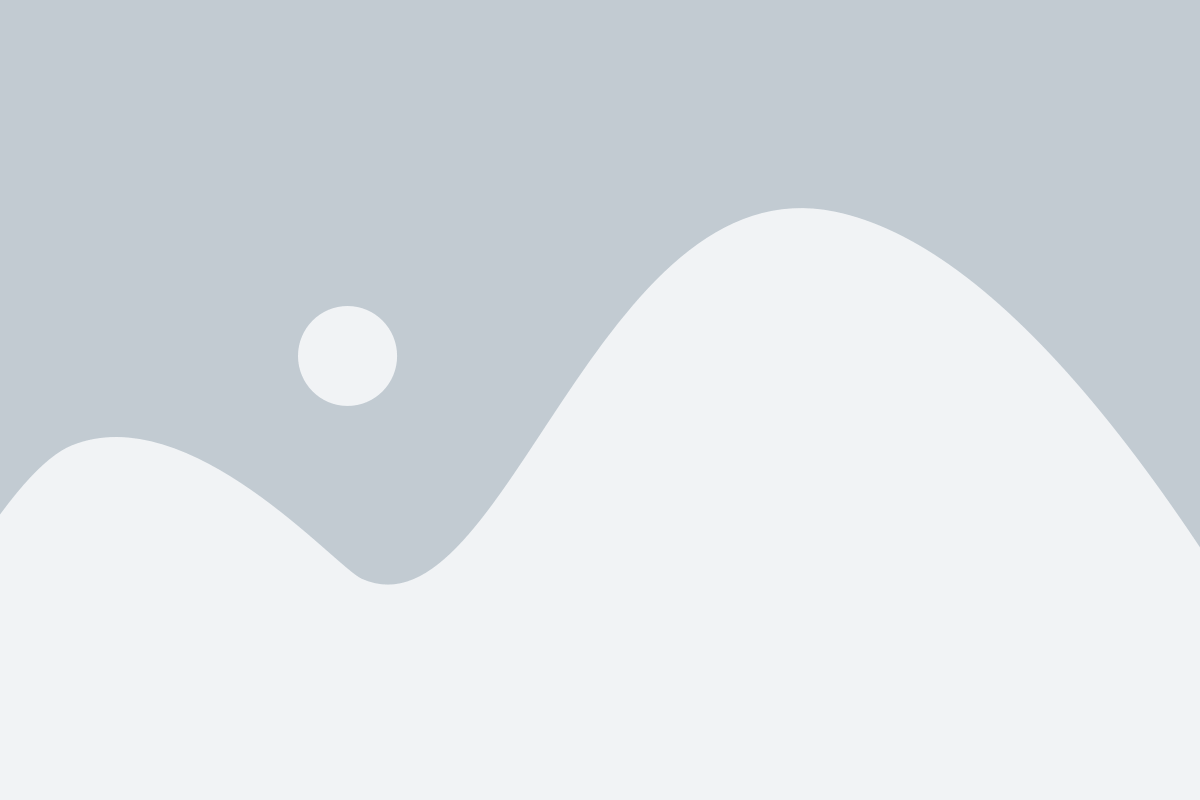
HIPS is easy to machine and offers good dimensional stability and impact resistance, suitable for prototyping and modeling.
- HIPS Board White
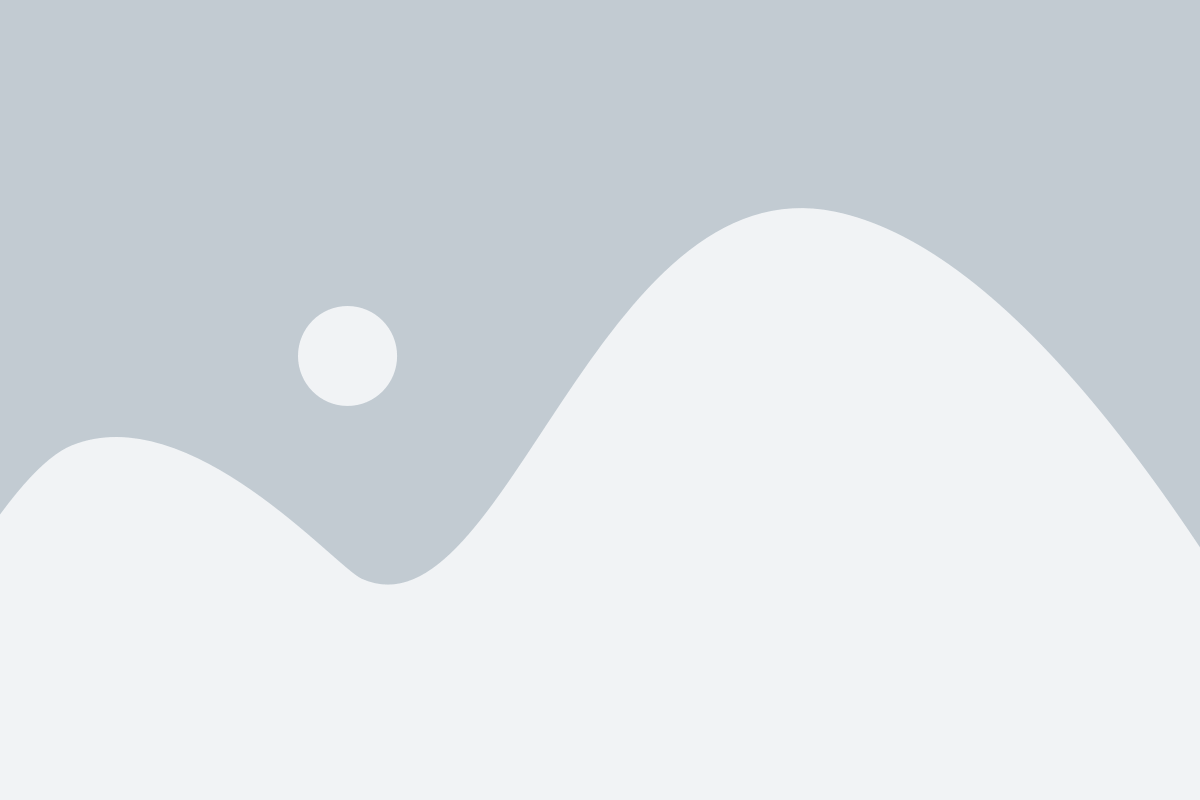
LDPE is soft, flexible, and used in applications where heat sealing is required, such as in tubing and plastic bags.
- LDPE White
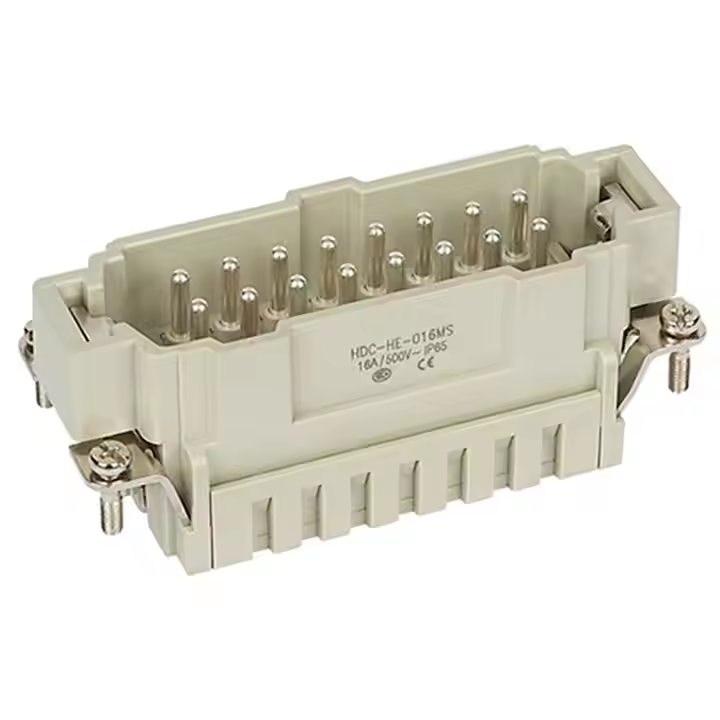
PBT is a strong, rigid plastic that is heat resistant and commonly used in electrical components and casings.
- PBT Black
- PBT Milky White(Natural)
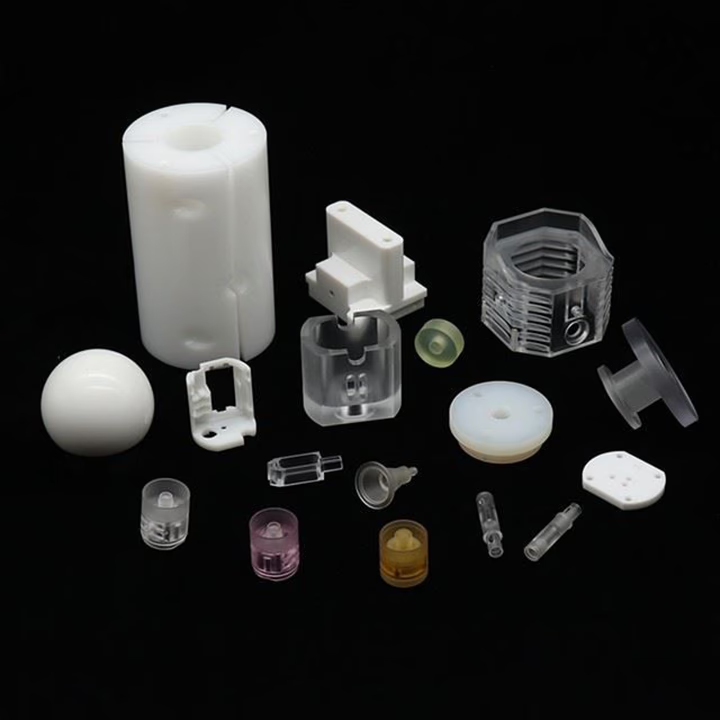
Like High-Performance Plastics, Engineering Plastics, Industrial Plastics, Biocompatible Materials, Food Safe Plastics, and Other Modified Thermoplastics. There are many other plastic or resin materials for different applications. Whether it’s on our material list or not, we could source them from a certified supplier for your project.
Insert Molding Capabilities
Standards | Description |
Maximum Part Size | 200×400×100mm 7.87×15.75×3.94 in. |
Manimum Part Size | 2×2×2mm 0.08×0.08×0.08in |
Substrate Wall Thickness | From 0.5 to 3mm From 0.20 to 0.12 in. |
Tolerance | +/- 0.025 mm |
Radii | 0.1mm |
Depth | 100mm from the parting line |
Mold Validation | Provide T0, T1, T2 samples before mass production |
Inspection and Certification Options | First Article Inspection, ISO 9001, ISO 13485 |
Lead Time | From mold making to sample delivery: 15-45 business days |
Advantages of Insert Molding
Overmolding enhances product durability and functionality by integrating different materials, offering improved grip, aesthetics, and cost-effective assembly.
- Eliminate assembly: Insert molded parts do not require assembly because there is only one manufacturing process.
- Reduce costs: The removal of the assembly process reduces the cost of the insert molding process compared to the standard injection molding.
- Reduced part size and weight: Insert molded parts that weigh less than all-metal parts.
- Improve part strength: Incorporating plastic and metal inserts increases the durability and strength of the parts compared to other injection molding processes.
Applications of Insert Molding
Plastic insert molding is a versatile process used across various industries to create both prototypes and fully functional products. Here are some key industrial applications:
- Consumer Goods: Custom plastic insert molding is ideal for manufacturing consumer goods, offering both functional and aesthetic enhancements. The process can be used to produce items such as kitchen utensils, electronics housings, and everyday tools.
- Medical Devices: Insert molding is critical in the medical industry, especially for creating devices and components that require biocompatibility. This includes medical implants, surgical instruments, and other healthcare products where precision and safety are paramount.
- Aerospace and Automotive: The process is well-suited for producing robust, durable components in the aerospace and automotive sectors. It is commonly used to create handheld devices like screwdrivers, scissors, dials, knobs, and other essential parts that must withstand harsh conditions.
- Communication Devices: Insert molding is also applied in the production of communication devices due to the need for strength and durability. Components for radios, smartphones, and other communication equipment benefit from the enhanced performance provided by insert molding.