Injection Mold Tooling Service
Get precise and outstanding custom injection molds to produce high-quality plastic parts. Tight Tolerance of 0.02 mm
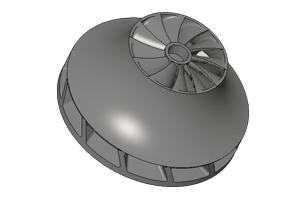
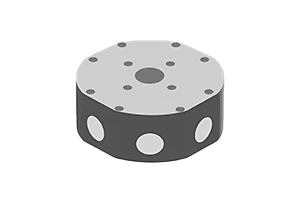
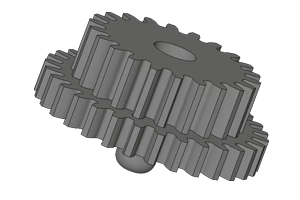
Start A New Injection Molding Quote
STEP | STP | SLDPRT | IPT | PRT | SAT files
- All uploads are secure and confidential.
What is Tooling in Injection Molding?
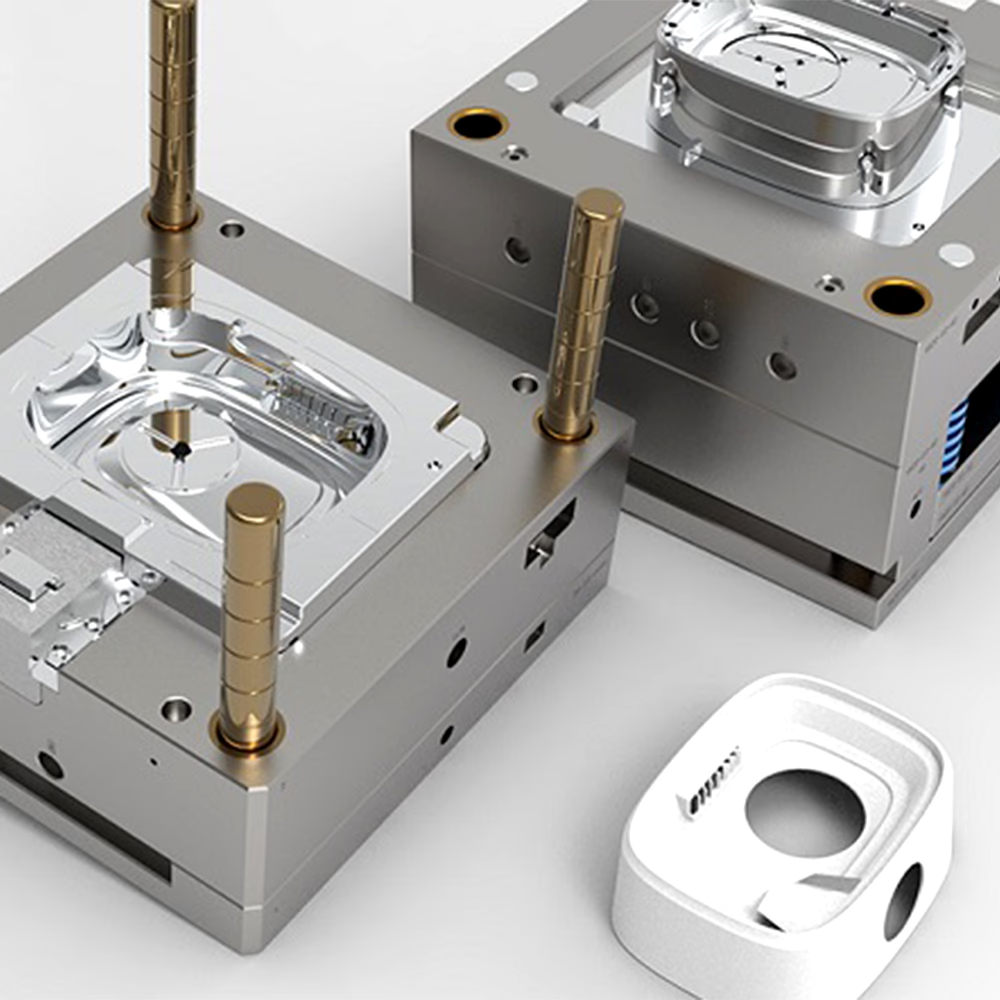
Experience cutting-edge custom injection molding with RapidTools. We collaborate closely with you to understand your project’s unique requirements and develop precise injection molds tailored to your specifications. Our skilled technicians manage every aspect of the mold production process, ensuring excellence in every detail.
Our flexible approach allows us to create both prototype tools and production molds efficiently and cost-effectively. With rapid lead times and optimized production capabilities, we help accelerate your path to market. Ready to elevate your plastic part production? RapidTools is here to support you every step of the way.
RapidTools Mold Tooling Services
PROTOTYPING
Rapid Tooling
Obtain swift design feedback and validation with our high-quality prototype tooling. At Arapidtools, we specialize in producing small batches of plastic molded parts with precise injection molding prototypes. Our expertise in manufacturing prototype molds within days ensures you can conduct functional tests and assess market interest effectively. We use affordable aluminum tooling to minimize financial risks before transitioning to full-scale production.
PRODUCTION
Production Tooling
We specialize in crafting high-quality production molds for large-scale plastic part manufacturing. Using high-strength, durable tool steel, our production tooling is built to produce hundreds of thousands of parts. We tailor materials and construction methods to meet your specific needs, ensuring optimal performance and longevity for your production molds.
Types of Injection Molds
We provide a wide range of injection mold tooling options tailored to your specifications and applications. Whether you need prototype mold tooling, production molds, or export molds, RapidTools is your trusted partner for delivering reliable and high-quality solutions.
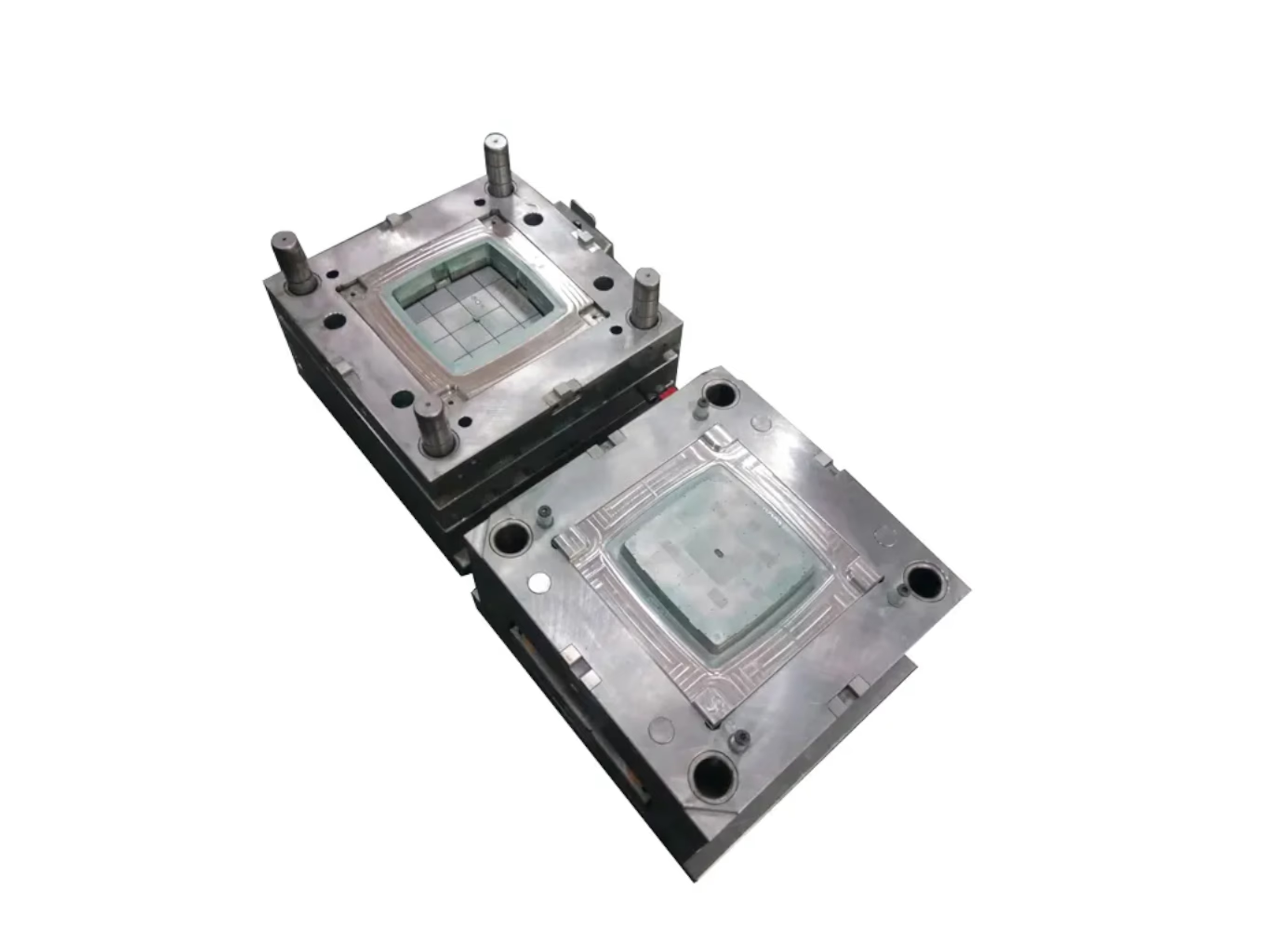
Single Cavity Mold
Ensure efficient low-volume plastic parts production with high-quality single cavity injection molds. These cost-effective tooling options provide greater control over the manufacturing process, making them ideal for precision-driven projects.
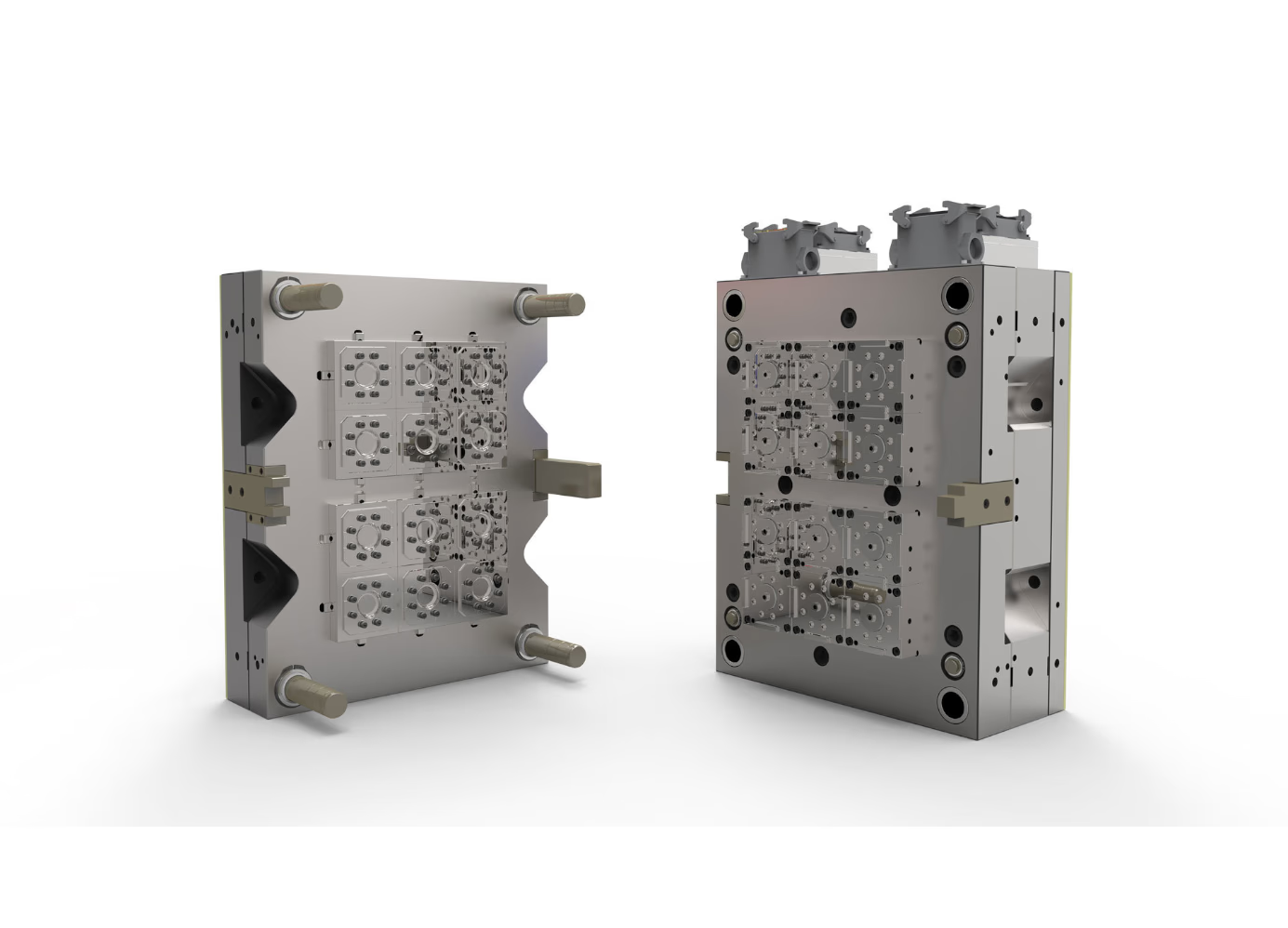
Multi Cavity Mold
Efficiently manufacture multiple plastic molded parts with superior-quality multi-cavity molds. Our multi-cavity injection molds ensure more effective use of cycle time while offering a lower cost of a unit part. With higher productivity, you can get high quantities of parts per cycle.
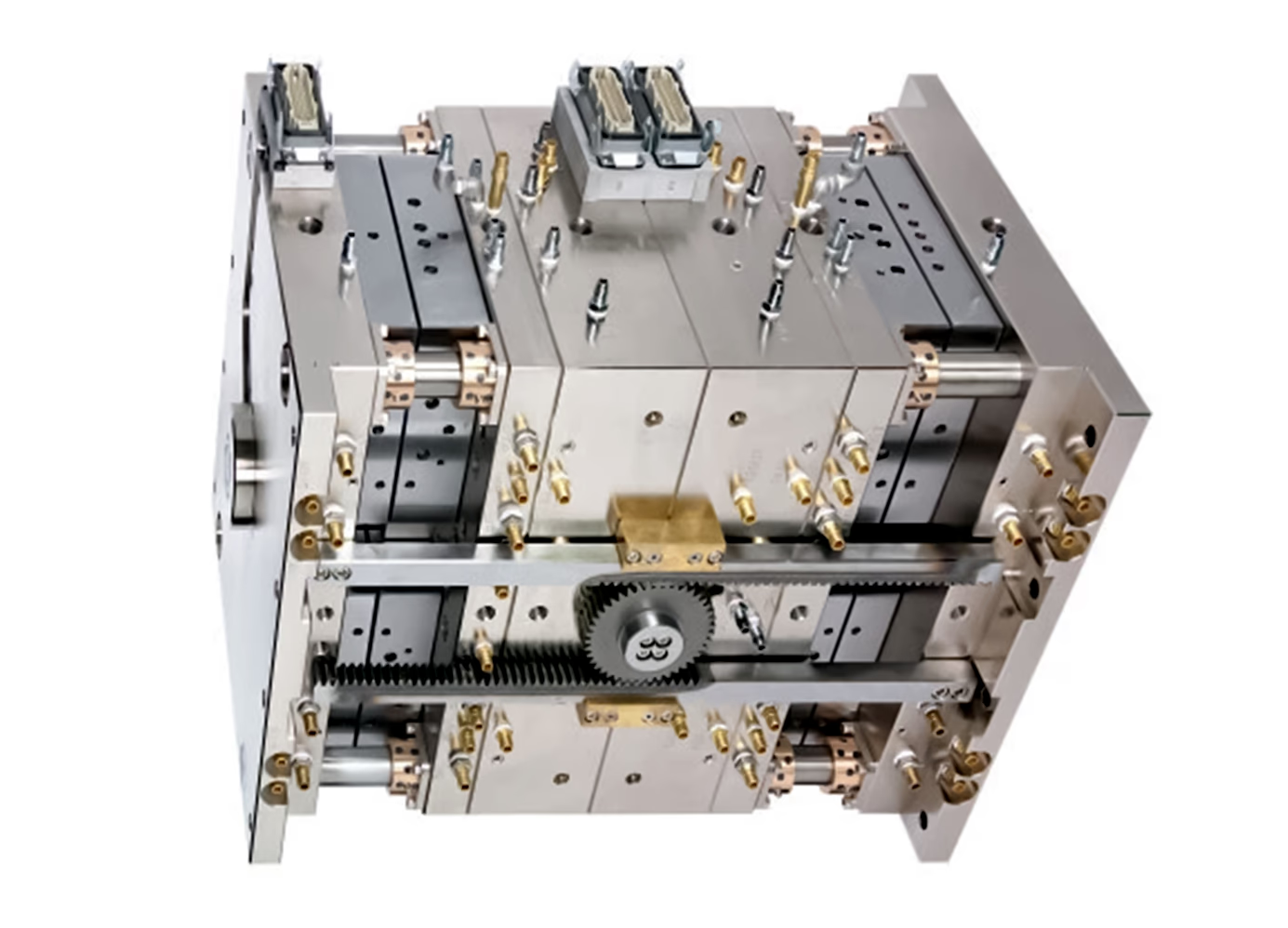
Stack Mold
Increase the output of your injection molding process with innovative stack molds. RapidTools delivers excellent stack mold tooling to increase your molding efficiency while reducing overall part cost. We can design stack molds with equal numbers or different numbers of cavities in each parting surface. Create multi-component assemblies in one shot!
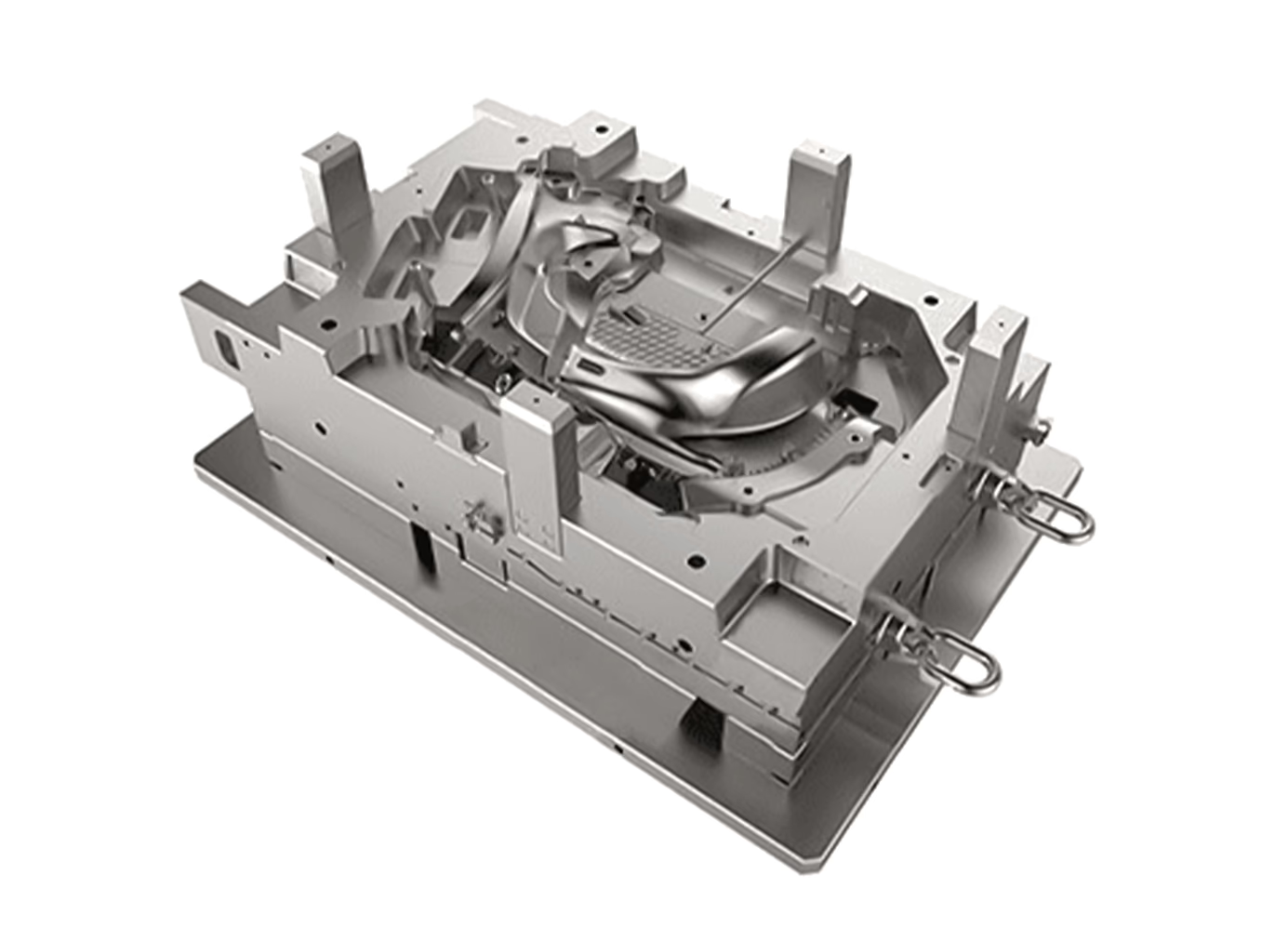
2K Injection Mold
Economical and efficient custom injection molding solution for molding two different plastic materials. We provide 2K injection mold tooling to allow a seamless combination of soft and hard plastics for one product. Save costs by creating tailor-made products and combining assembly steps into one molding process.
Materials for Injection Mold
Tool Steel
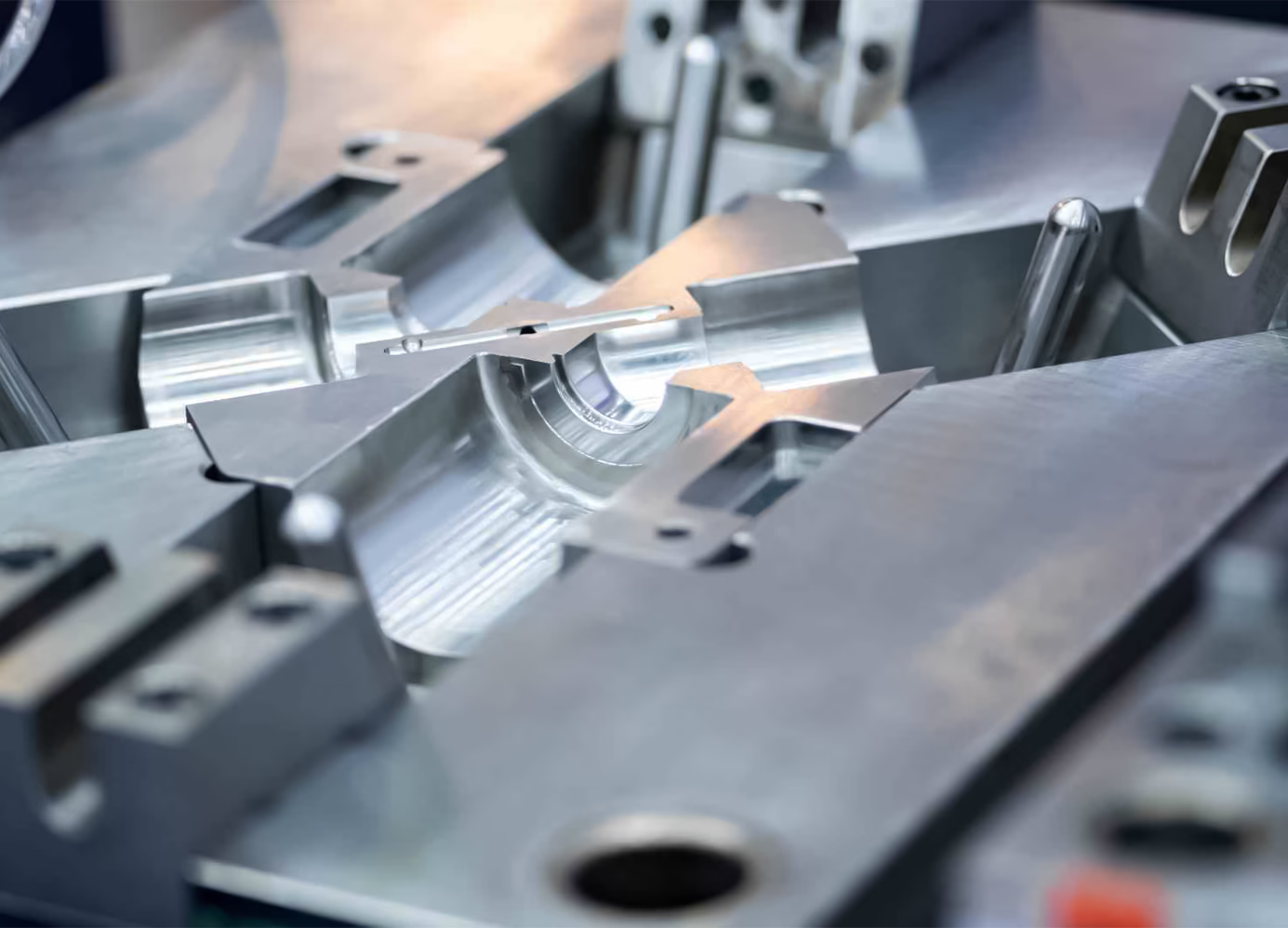
Before starting the injection molding process for either low or high-volume production, precise CNC-machined tooling is essential. The tooling is typically made from high-tolerance materials like tool steel to ensure durability and accuracy. Commonly used tool steel.
Types include P20, H13, S7, NAK80, S136, S136H, 718, 718H, and 738.
Stainless Steel
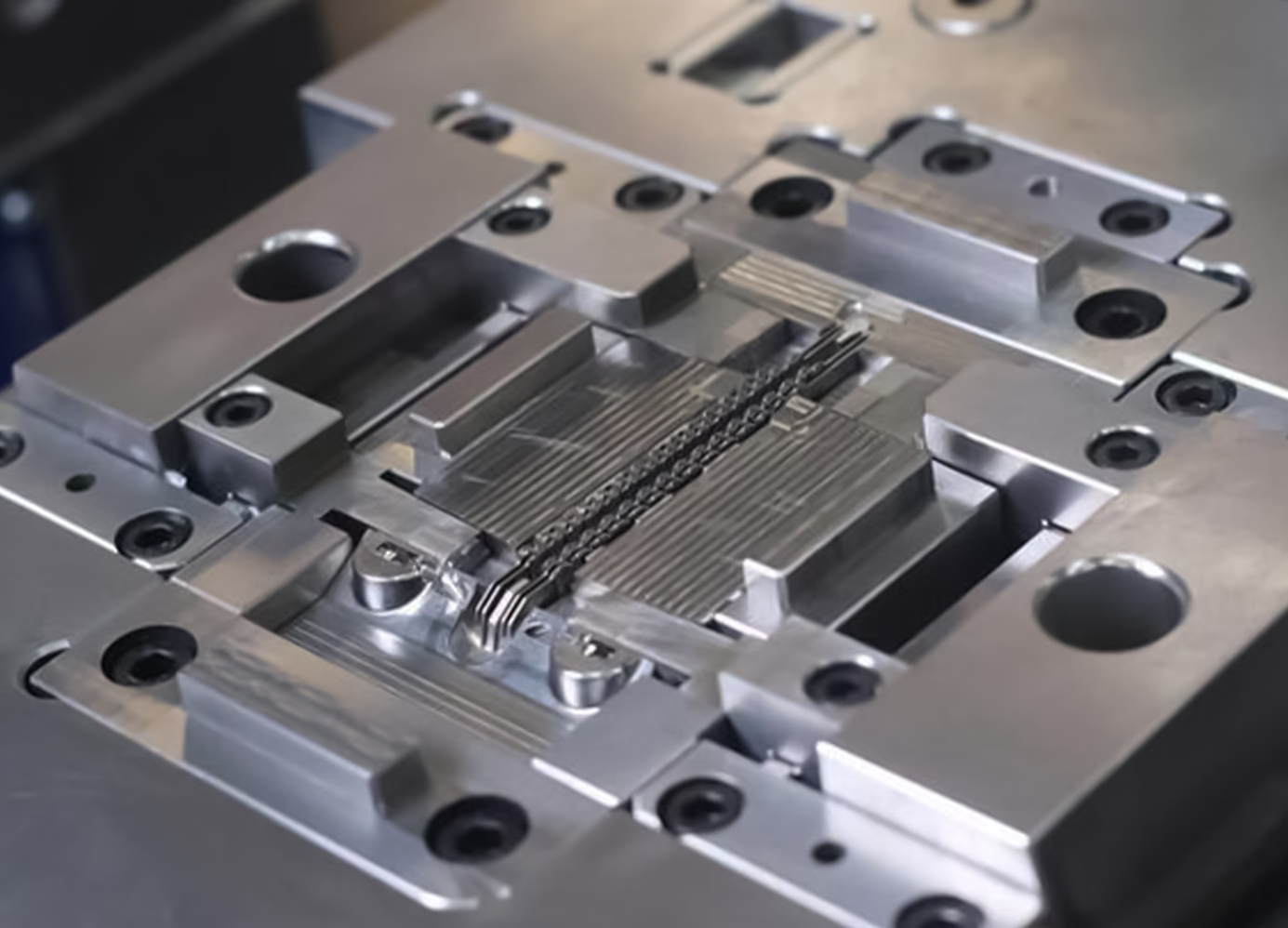
Injection molds are created from steel and stainless steel, which are costly to manufacture. Due to their expense, these molds are typically used only in large-scale productions.
Types: 420, NAK80, S136, 316L, 316, 301, 303, 304
Aluminum
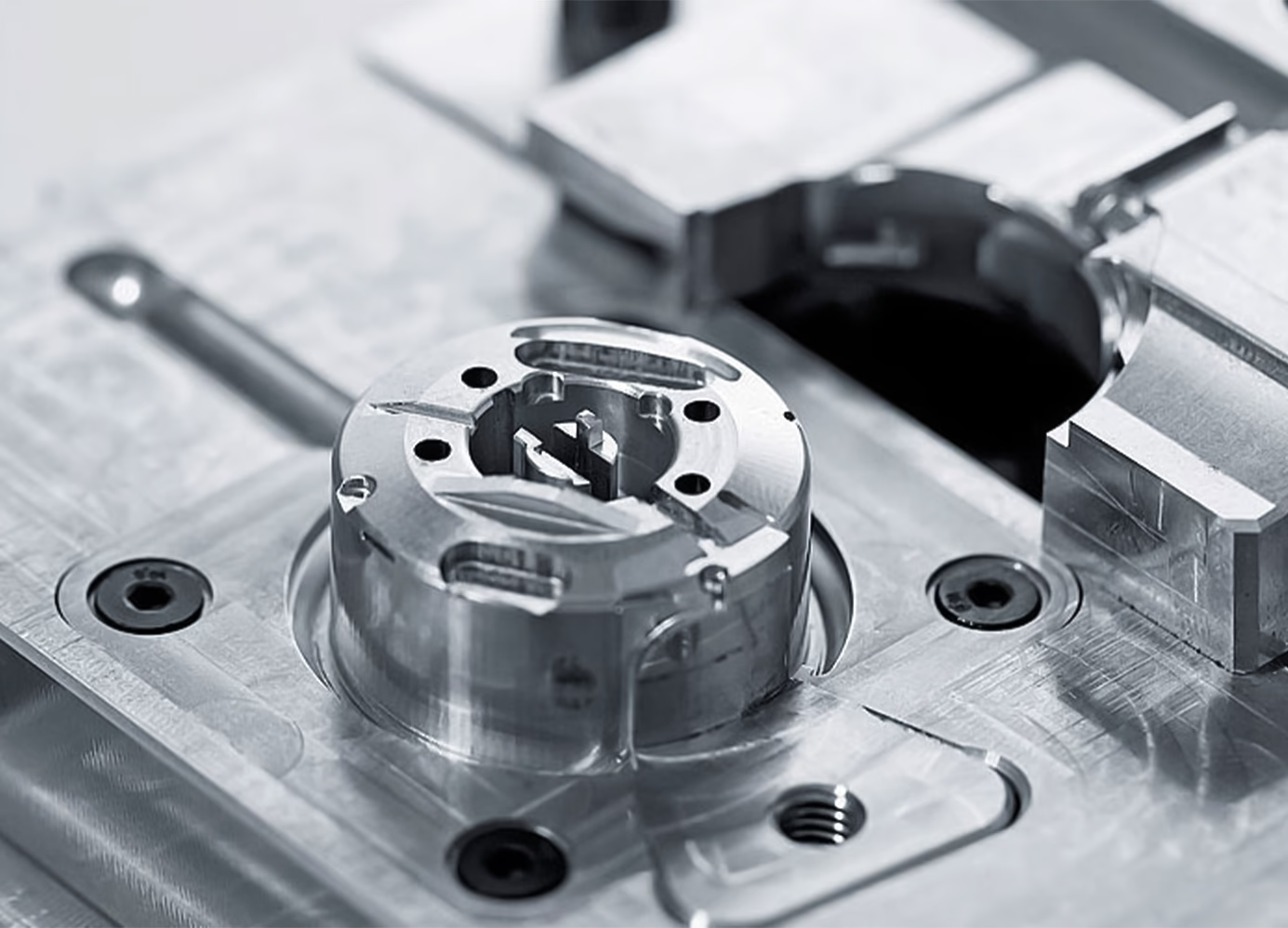
Aluminum molds are significantly more affordable than traditional steel and carbon steel injection molds. They provide faster cycle times and quicker turnarounds, making them ideal for testing markets and accelerating product development.
Types: 6061, 5052, 7075
Injection Molding Capabilities
At RapidTools, we specialize in designing and manufacturing precise custom injection molds using high-quality materials. Our processes deliver unmatched consistency and repeatability, with fast lead times and competitive pricing. Every plastic injection mold we produce adheres to international standards, ensuring durability and reliability for one-off projects, small batches, and large-scale production tooling.
Purpose | Shot Life | Tolerance | Cost | Lead Time | |
Class 105 | Prototype Testing | Under 500 cycles | ± 0.02mm | $ | 7-10 days |
Class 104 | Low-volume Production | Under 100.000 cycles | ± 0.02mm | $$$ | 10-15 days |
Class 103 | Low-volume Production | Under 500.000 cycles | ± 0.02mm | $$$$ | 10-15 days |
Class 102 | Medium-volume Production | Medium-volume Production | ± 0.02mm | $$$$$ | 10-15 days |
Class 101 | High-volume Production | Over 1,000,000 cycles | ± 0.02mm | $$$$$$ | 10-18 days |
Plastic Injection Molding Process
Plastic injection molding is a highly efficient and versatile process used to produce complex and intricate plastic parts through the following steps
- Mold Design & Material: Molds are precision-designed using CAD software, typically crafted from steel for durability or aluminum for faster cooling, depending on production requirements.
- Plastic Preparation: Specific plastic granules are selected based on desired product properties, then dried and loaded into the machine’s hopper.
- Melting & Injection: The plastic is melted and injected into the mold under high pressure, ensuring complete filling and accurate detailing.
- Cooling & Solidification: The molten plastic cools and solidifies within the mold, aided by precisely controlled cooling channels to minimize defects.
- Ejection & Finishing: The solidified part is ejected from the mold and may undergo trimming, polishing, or painting for final finishing.
- Quality Inspection: Each part is inspected to ensure it meets all required specifications for dimensions, appearance, and performance.
Advantages of Prototype Tool
Prototype tooling is crucial for efficient product development, providing a cost-effective and quick route from design to functional prototype. Its key advantages include:
- Speed to Market: Accelerates development and refinement, shortening the time to launch.
- Cost Efficiency: More affordable than full-scale molds, reducing initial investment.
- Design Flexibility: Allows easy modifications based on testing feedback.
- Risk Reduction: Identifies potential production issues early, preventing costly future corrections.
- Functional Testing: Enables thorough testing to ensure the product meets all requirements.
Injection Mold Tooling FAQs
Why is Injection Molding Tooling So Expensive?
Injection molding tooling costs are high for various reasons.
Material Costs: Molds are typically made from high-quality, durable materials like hardened steel or aluminum. Steel is particularly costly but necessary for long production runs due to its durability.
Complex Manufacturing Process: Producing molds involves precise and labor-intensive processes, including CNC machining, EDM (Electrical Discharge Machining), and sometimes hand polishing. The complexity of the mold, including multiple cavities, undercuts, or intricate details, adds to the cost.
Precision: High-precision molds are essential for producing parts with tight tolerances, especially in industries like automotive, aerospace, or medical. Achieving this level of precision requires advanced manufacturing equipment and skilled technicians, which increases the overall cost.
Customization: Injection molds are custom-built for specific products, and each design demands unique considerations. This custom nature of the tooling, tailored to individual part requirements, significantly raises costs compared to more standard, off-the-shelf tools.
Design and Engineering Time: Developing a mold requires significant design work to ensure it can withstand high pressure and temperature during the injection process. The design must also account for part geometry, cooling channels, and ejection systems, requiring specialized engineering expertise.
What Factors Influence Injection Mold Tooling Design?
Several factors affect the design:
Part Design and Geometry: The shape, size, and complexity of the part being molded greatly influence the mold design. Complex geometries, intricate details, and thin walls require specialized mold features, such as additional cooling channels or more advanced gating systems.
Material Selection: The plastic type significantly impacts mold design, affecting factors like cooling rates, shrinkage, and flow behavior. For example, polypropylene shrinks more, while polycarbonate requires higher mold temperatures. The mold material must also resist wear from abrasive or corrosive plastics.
Tolerances: Tolerances and Precision Requirements: High-precision parts require molds with tighter tolerances, which can complicate the design and increase manufacturing costs. Mold designers must account for dimensional accuracy and consistency, particularly in industries like automotive and medical.
Ejection System: The method of ejecting the part from the mold affects both mold design and cycle time. Options like ejector pins, air blast systems, or stripper plates must be carefully integrated into the mold to avoid damaging the part.
Gate Design: The location and type of gate (direct, pin, or edge gate) determine how the molten plastic enters the mold. Gate design affects the quality of the finished part, influencing flow characteristics, surface finish, and cycle time.
Undercuts and Parting Lines: Parts with undercuts or complex geometries may require side actions or lifters in the mold design to release the part without damaging it. These features increase mold complexity and cost.
Let's Start A New Project Today