Custom Online CNC Turning Services
We offer custom CNC turning services with fast lead times and competitive pricing, ranging from rapid prototyping to production runs. Our precision machining achieves tight tolerances of 0.005 mm, with lead times as quick as 1 day.
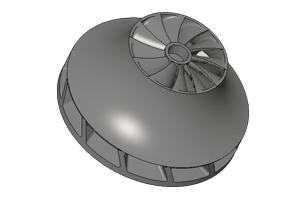
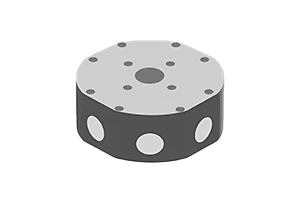
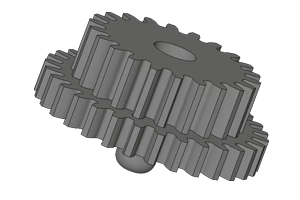
Start A New CNC Quote
STEP | STP | SLDPRT | IPT | PRT | SAT files
- All uploads are secure and confidential.
CNC Turning With RapidTools
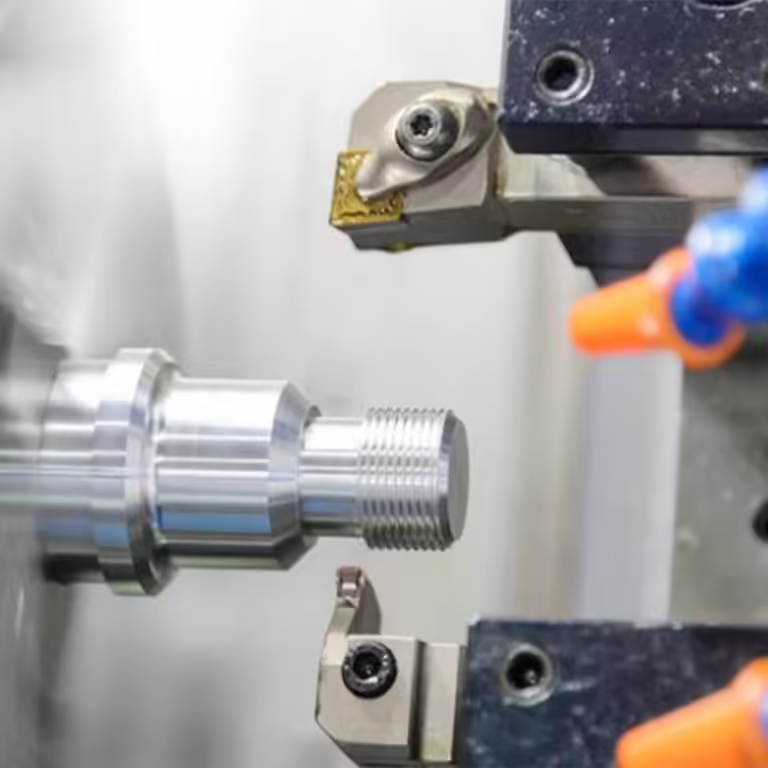
Take advantage of our on-demand CNC turning service for reliable metal and plastic turned parts tailored to your unique projects. With advanced technologies and skilled technicians, RapidDirect produces high-quality custom prototypes and end-use production parts, delivering high accuracy even for complex designs. Enjoy durable parts with features ranging from flats to radial and axial holes, slots, and grooves in as fast as one day.
Our precision CNC turning lathes offer low-cost solutions for both simple and complex cylindrical geometries. Utilizing live tooling, we create precise, intricate features like axial and radial holes, grooves, slots, and flats. The full automation of these versatile machines allows us to produce hundreds of parts with similar dimensions efficiently and cost-effectively.
Arapidtools CNC Turning Solutions
PROTOTYPING
Rapid Prototyping
Accelerate your product development with our rapid machining services. We specialize in the quick production of high-quality prototypes and mold tooling, offering fast turnaround times to support your design verification process.
PRODUCTION
Low and High-Volume Production
Whether you require small batches or large-scale production, we’ve got you covered. With strict tolerance controls and extensive capabilities, we adapt to your volume needs while maintaining the highest quality standards.
CNC Turning Materials
Our CNC turning processes accommodate a wide range of materials, including machine-grade metals and plastics. Whether you require precise turning of aluminum parts or other materials, we can deliver accurate rapid prototypes and low-volume production runs tailored to your needs. Explore some of the common materials for your CNC turning projects.
CNC Turning Metals
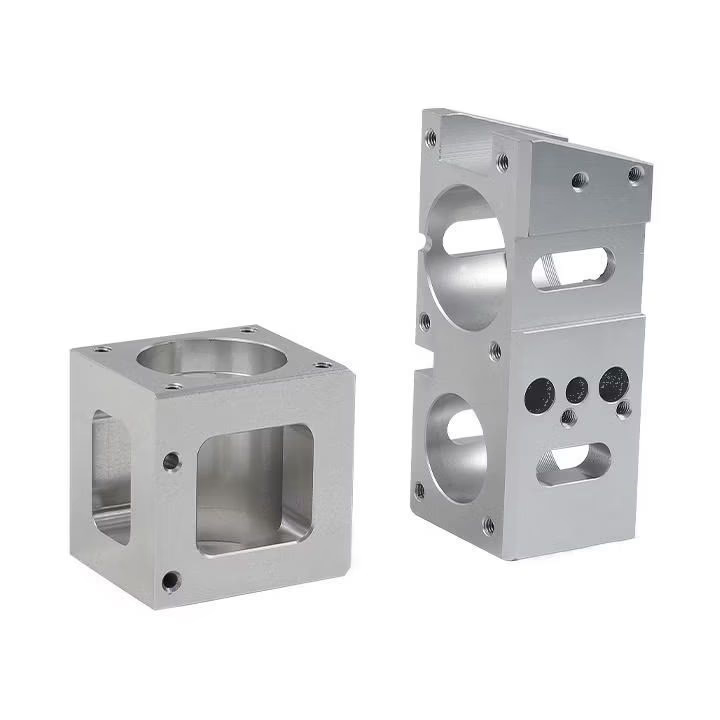
Aluminum is lightweight yet strong, with excellent machinability and corrosion resistance. Ideal for aerospace and automotive parts.
Alloys
- Aluminum 6061, 6061-T6
- Aluminum 2024
- Aluminum 5052
- Aluminum 5083
- Aluminum 6063
- Aluminum 6082
- Aluminum 7075, 7075-T6
- Aluminum ADC12 (A380)
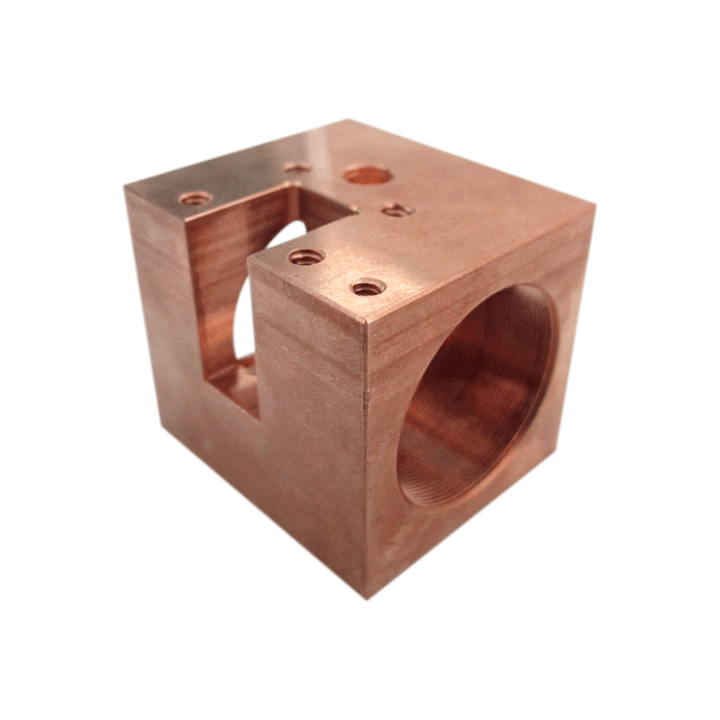
Copper is known for its superior electrical conductivity and thermal properties, making it perfect for electrical components and heat exchangers.
Alloys
- Copper C101(T2)
- Copper C103(T1)
- Copper C103(TU2)
- Copper C110(TU0)
- Beryllium Copper
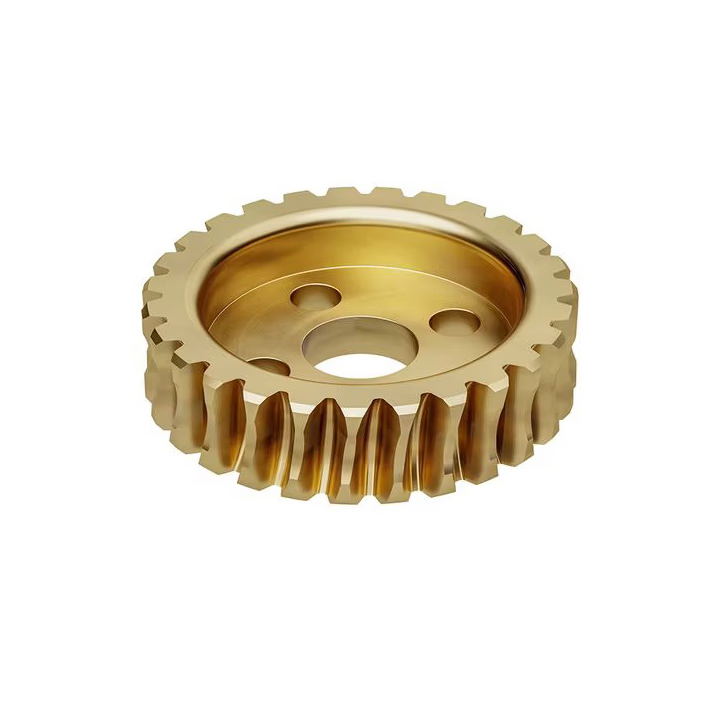
Brass is durable and has a low friction coefficient, which makes it suitable for fittings, tools, and musical instruments that require precision.
Alloys
- Brass C27400
- Brass C28000
- Brass C36000
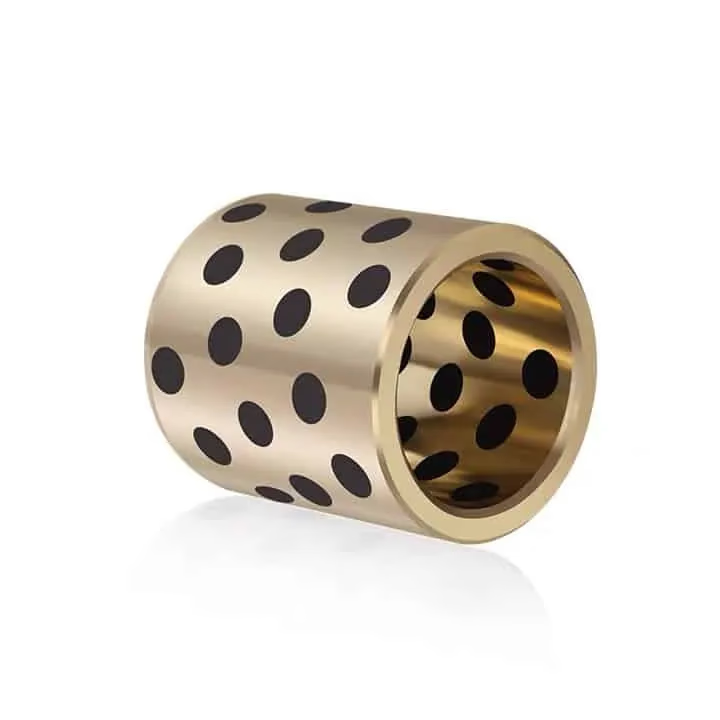
Bronze is highly resistant to corrosion and metal fatigue, favored for bearings, bushings, and marine hardware.
Alloys
- Tin Bronze
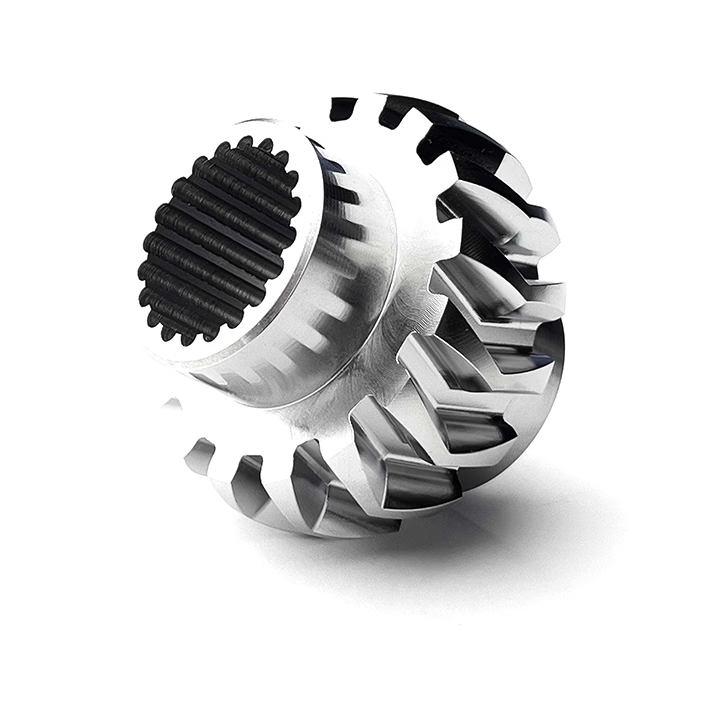
Steel is an alloy with high tensile strength and durability, commonly used in construction and automotive industries for its robustness.
Alloys
- Steel 1018, 1020, 1025, 1045, 1215, 4130, 4140, 4340, 5140, A36
- Die steel
- Alloy steel
- Chisel tool steel
- Spring steel
- High speed steel
- Cold rolled steel
- Bearing steel
- SPCC
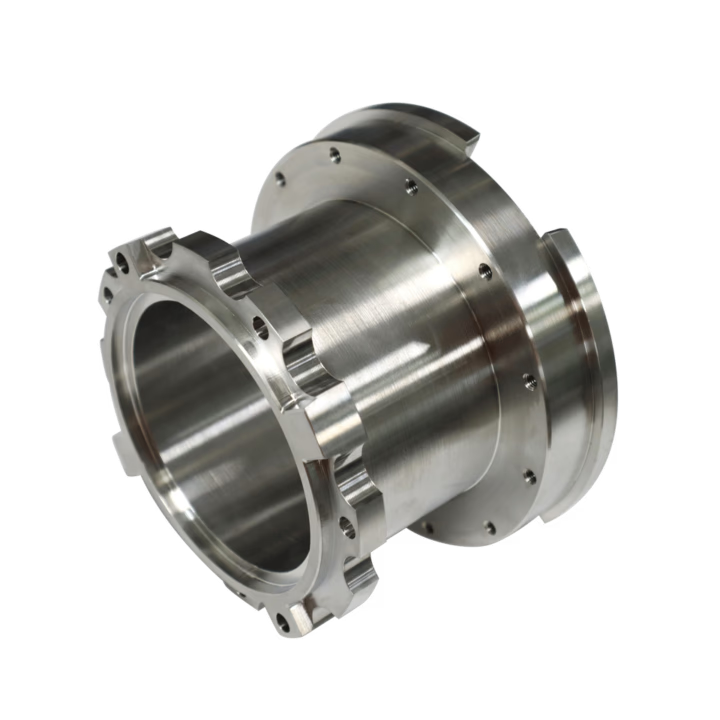
Stainless steel is renowned for its corrosion resistance, making it a prime choice for medical devices and food processing equipment.
Alloys
- Stainless Steel SUS201
- Stainless Steel SUS303
- Stainless Steel SUS 304
- Stainless Steel SUS316
- Stainless Steel SUS316L
- Stainless Steel SUS420
- Stainless Steel SUS430
- Stainless Steel SUS431
- Stainless Steel SUS440C
- Stainless Steel SUS630/17-4PH
- Stainless Steel AISI 304
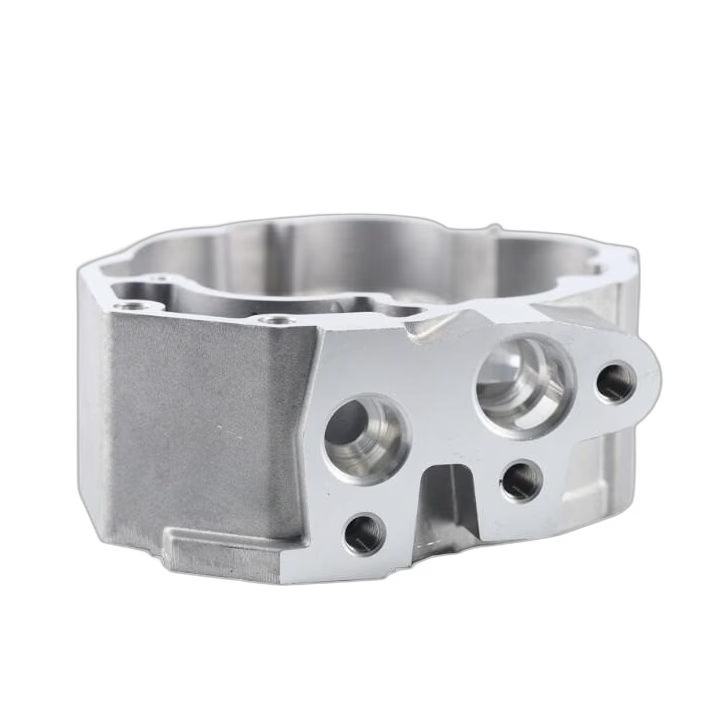
Magnesium is the lightest structural metal, offering high strength-to-weight ratios, perfect for automotive and aerospace applications where weight is critical.
Alloys
- Magnesium Alloy AZ31B
- Magnesium Alloy AZ91D
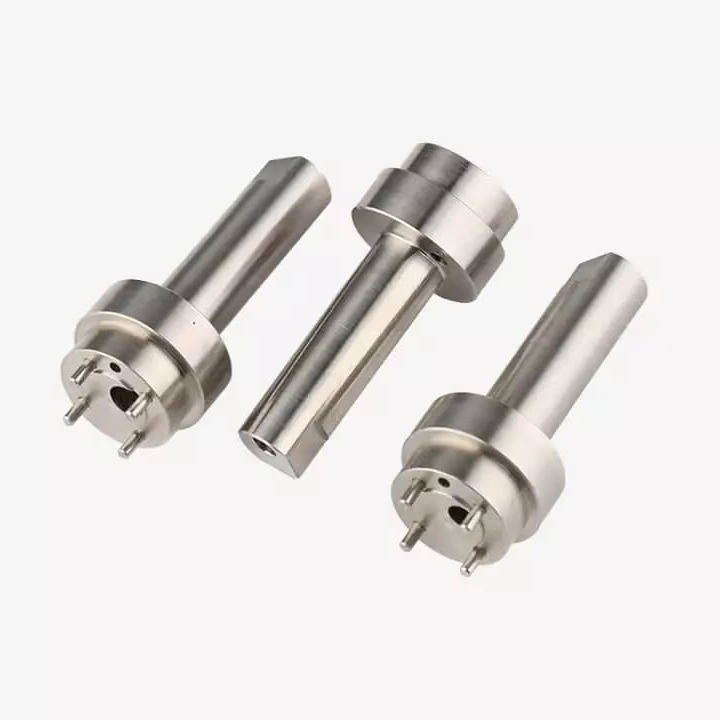
Titanium boasts the highest strength-to-density ratio among metals, highly resistant to corrosion and fatigue, ideal for aerospace, medical, and marine applications.
Alloys
- Titanium Alloy TA1
- Titanium Alloy TA2
- Titanium Alloy TC4/Ti-6Al 4V
CNC Turning Plastics
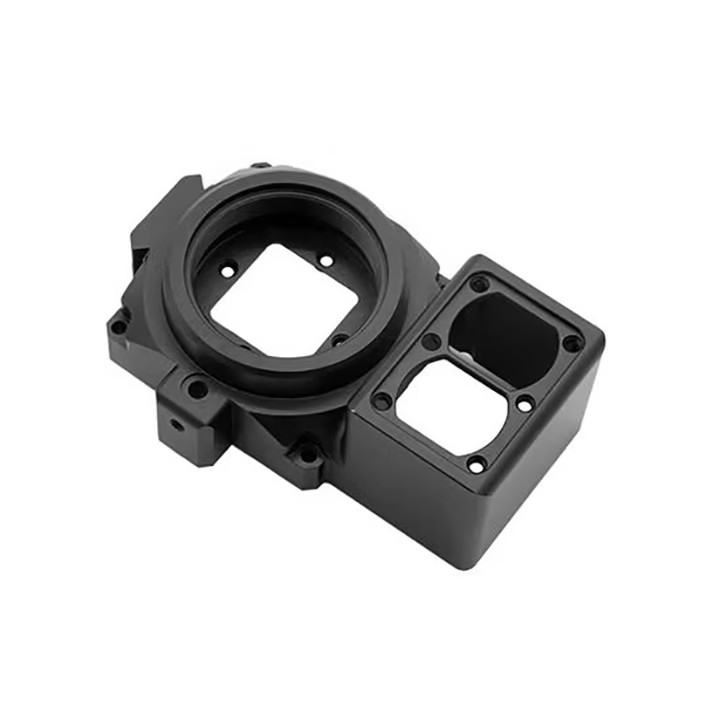
ABS is strong, durable, and offers good resistance to heat and impact. It’s preferred for automotive components and consumer goods.
- ABS Beige(Natural)
- ABS Black
- ABS Black Antistatic
- ABS Milky White
- ABS+PC Black
- ABS+PC White
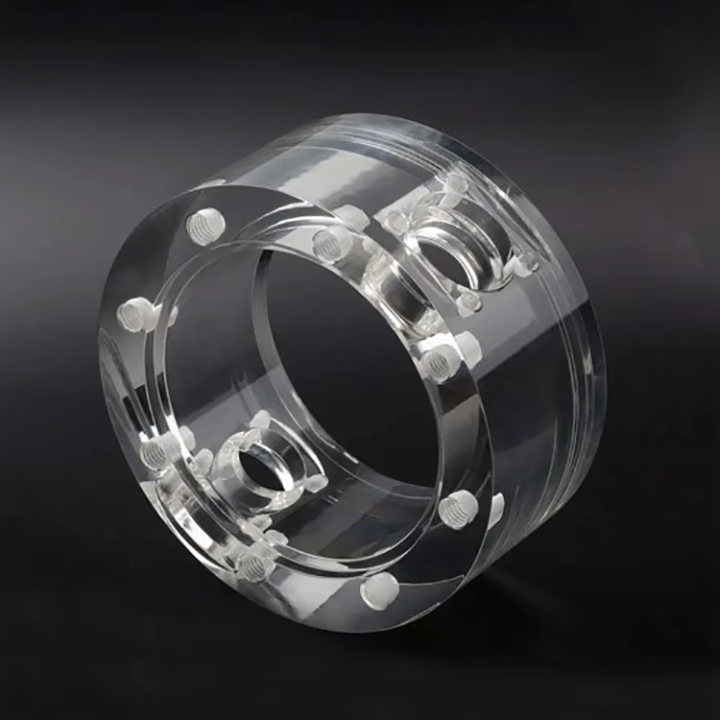
Polycarbonate is extremely durable and has high impact resistance, along with excellent clarity, used for bullet-proof glass and protective gear.
- PC Black
- PC Transparent
- PC White
- PC Yellowish White
- PC+GF30 Black
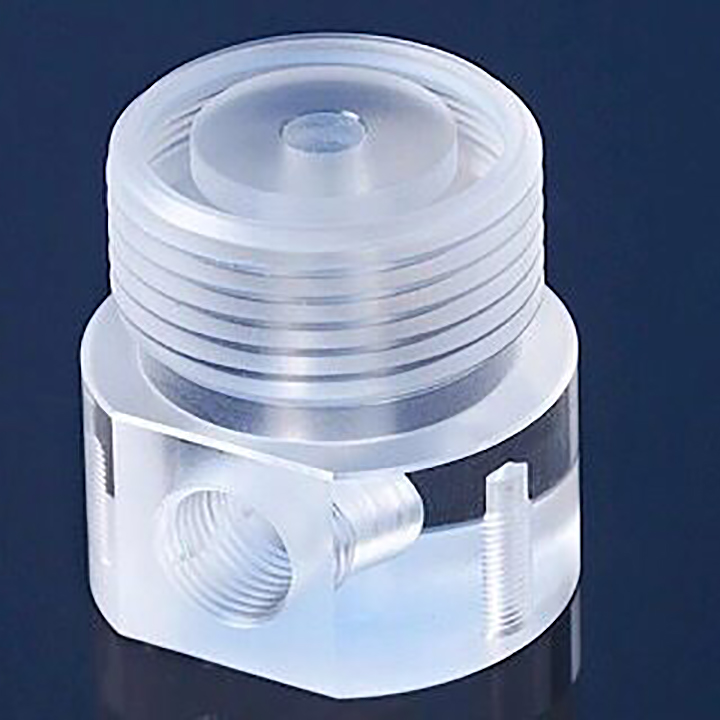
PMMA, or acrylic, is known for its crystal clarity and weather resistance, making it ideal for outdoor fixtures and display cases.
- PMMA Black
- PMMA Transparent
- PMMA White
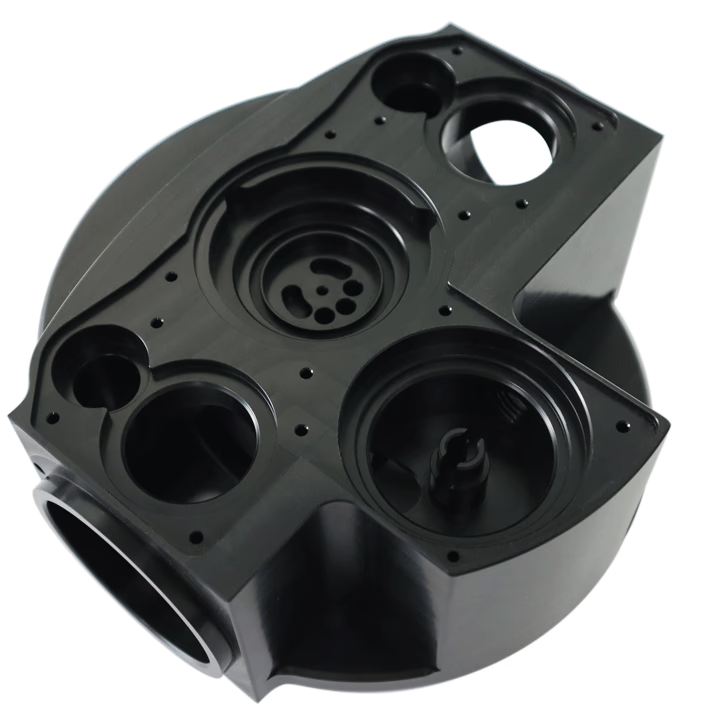
POM is strong, with a low friction surface and good dimensional stability, perfect for precision parts in mechanical applications.
- Dark brown (coffee) POM 100AF
- POM Black
- POM Blue
- POM White
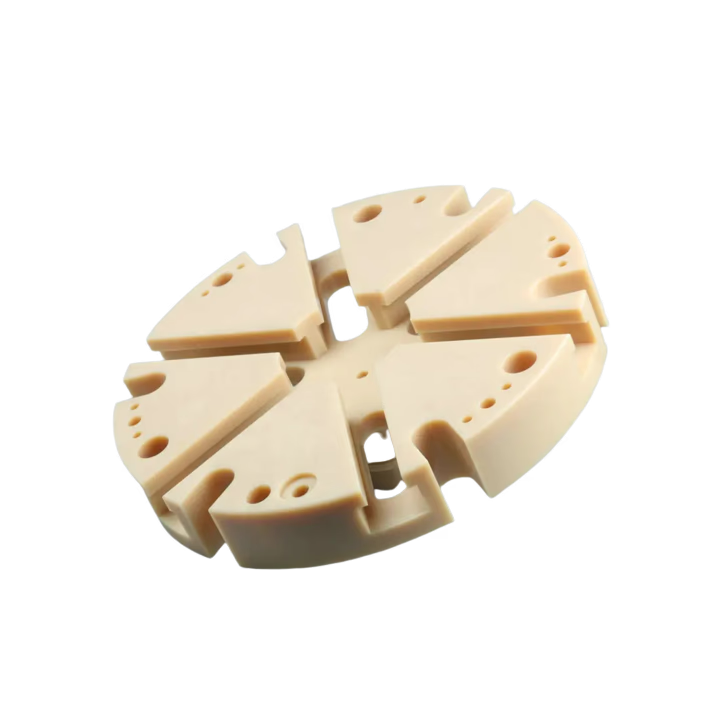
Nylon is versatile, strong, and wears well against friction, commonly used for gears, bearings, and other wear-resistant surfaces.
- PA(Nylon) Blue
- PA6 (Nylon)+GF15 Black
- PA6 (Nylon)+GF30 Black
- PA66 (Nylon) Beige(Natural)
- PA66 (Nylon) Black
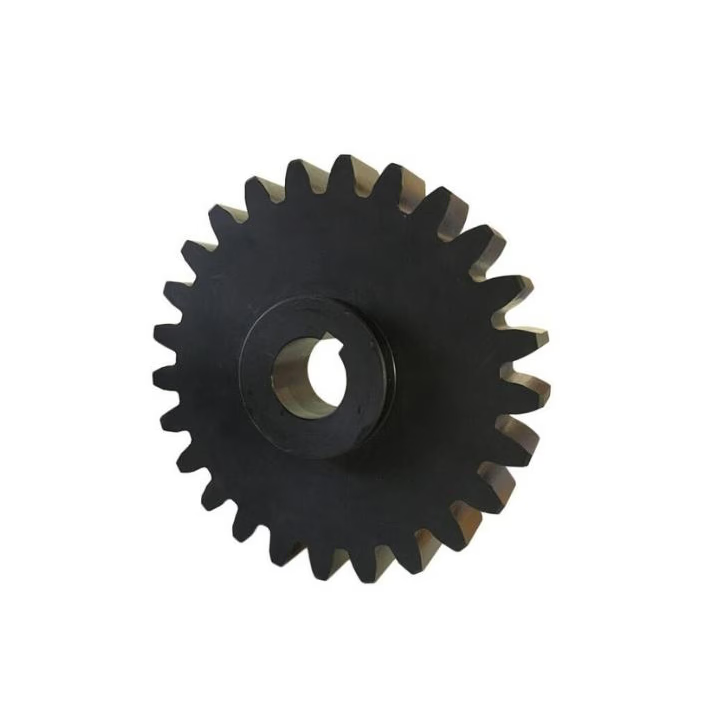
Polyethylene is lightweight and has high resistance to impact, widely used in packaging and containers.
- PE Black
- PE White

PEEK is renowned for its high temperature resistance and strength, often used in aerospace and medical implant manufacturing.
- PEEK Beige(Natural)
- PEEK Black
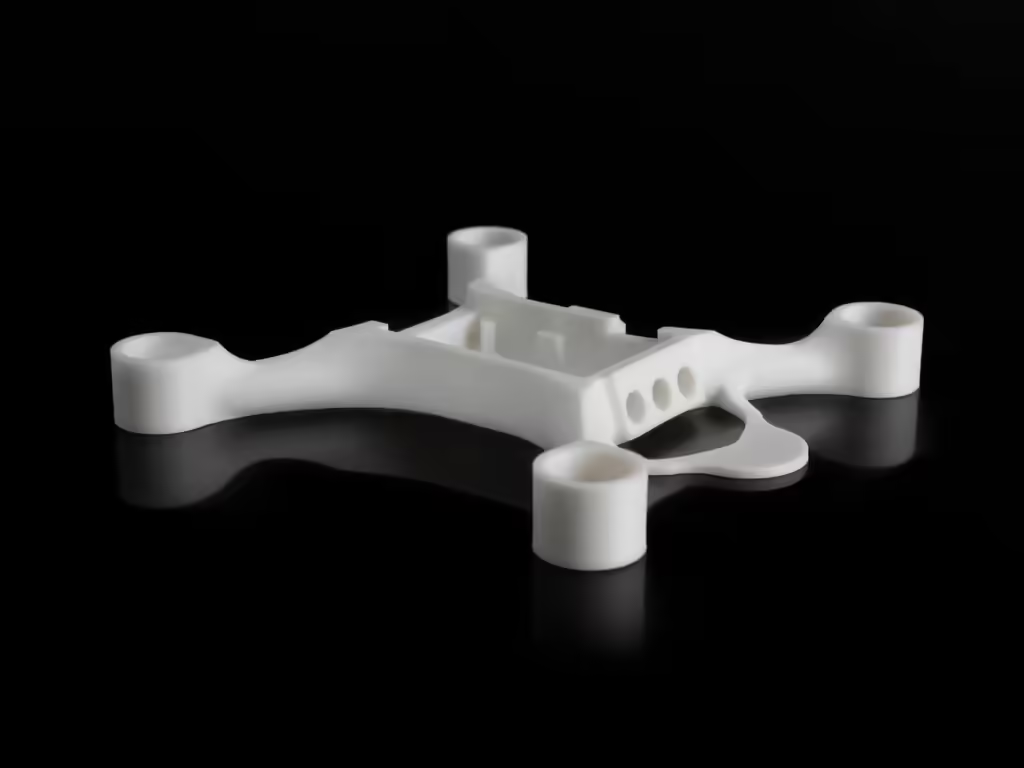
Polypropylene is tough, has excellent chemical resistance, and is used for automotive parts, containers, and in packaging.
- PP Black
- PP White
- PP+GF30 Black

HDPE is known for its high strength-to-density ratio, resistance to impacts, and is used in making bottles and corrosion-resistant piping.
- HDPE Black
- HDPE White
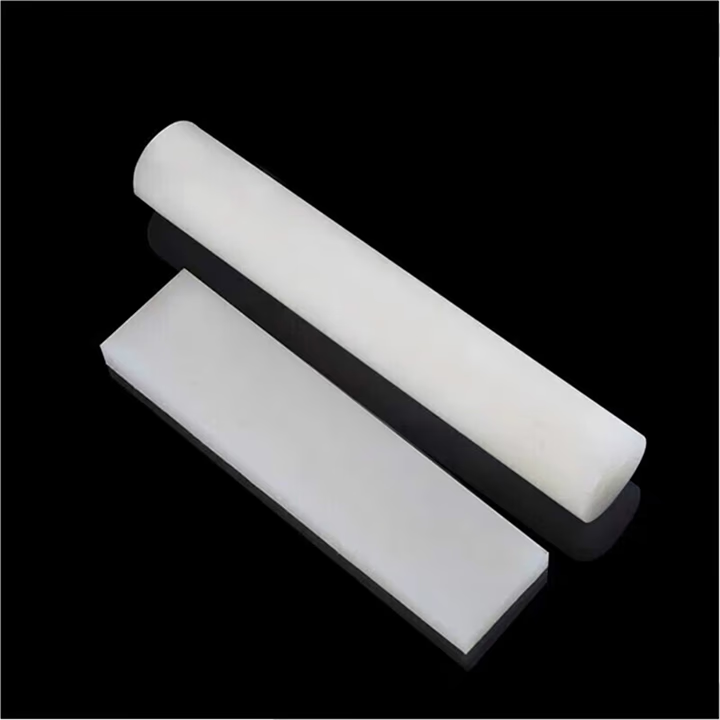
HIPS is easy to machine and offers good dimensional stability and impact resistance, suitable for prototyping and modeling.
- HIPS Board White
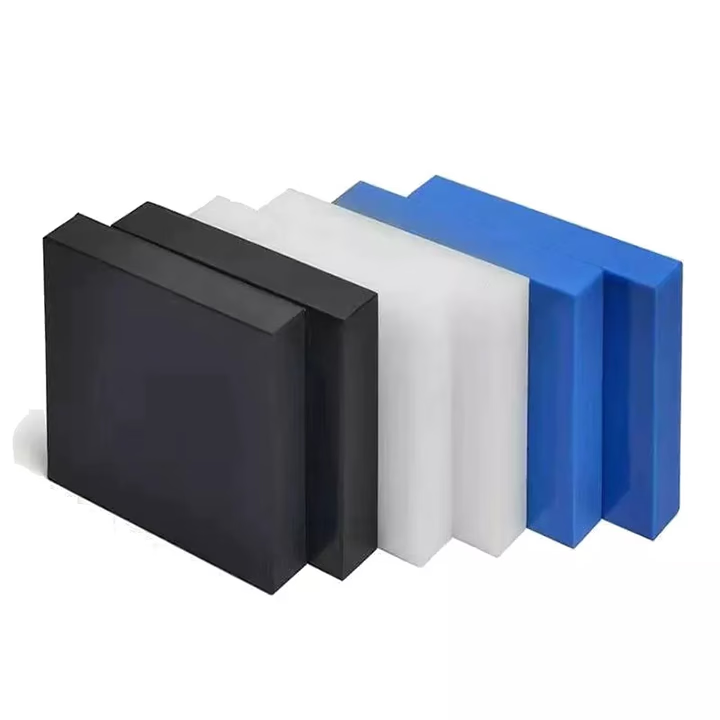
LDPE is soft, flexible, and used in applications where heat sealing is required, such as in tubing and plastic bags.
- LDPE White
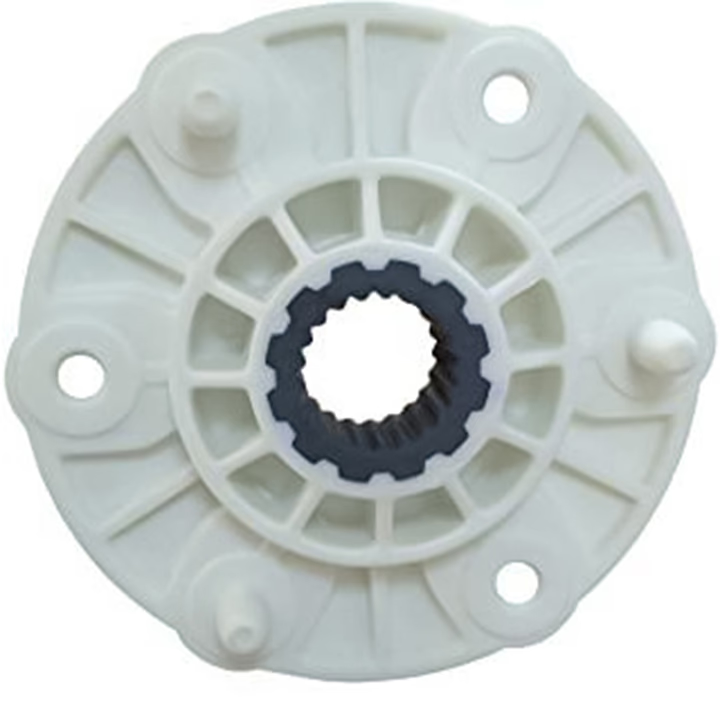
PBT is a strong, rigid plastic that is heat resistant and commonly used in electrical components and casings.
- PBT Black
- PBT Milky White(Natural)
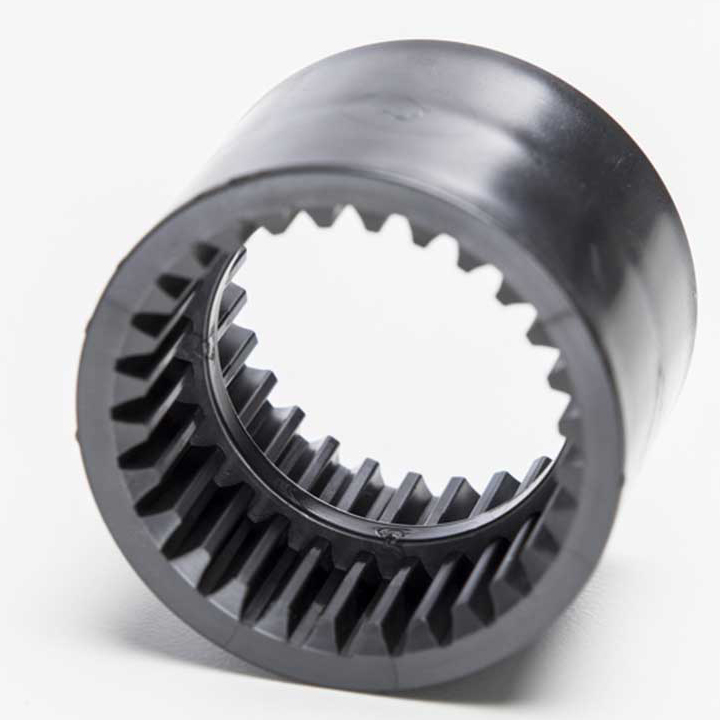
PPA offers high heat resistance and stiffness, ideal for automotive and electrical applications that require durability at high temperatures.
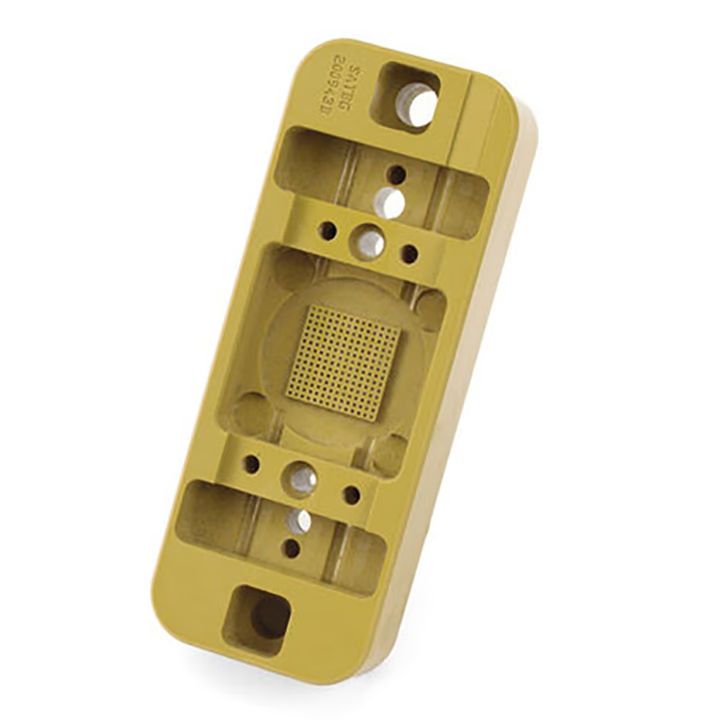
PAI has exceptional thermal and chemical stability, used in high-performance parts in aerospace and automotive sectors.
- PAI Brown
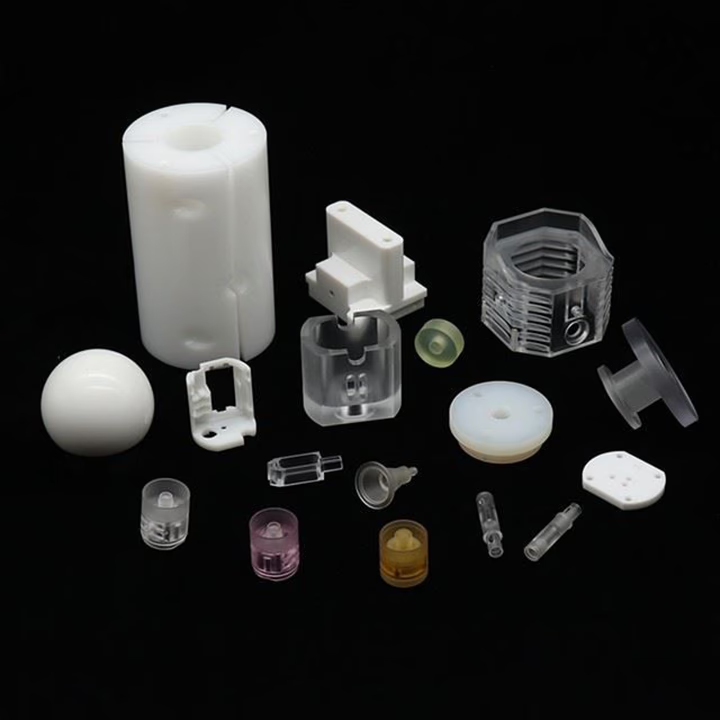
For Example: High Performance Plastics, Engineering Plastics, Industrial Plastics, Biocompatible Materials, Food Safe Plastics, and Other Modified Thermoplastics.
CNC Turning Surface Finishes
Attain the ideal finish with our selection of surface treatments. Whether you need anodizing, plating, or painting, we ensure your parts meet both aesthetic and functional requirements.
As Machined
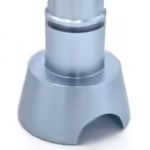
Anodizing
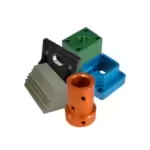
Anodizing increases corrosion resistance and wear properties, while allowing for color dyeing, ideal for aluminum parts.
Polishing
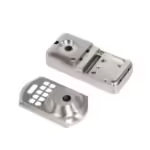
Polishing achieves a high gloss finish, reducing surface roughness and enhancing the aesthetic appeal of metals.
Sand Blasting
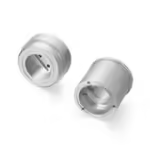
Sand blasting uses pressurized sand or other media to clean and texture the surface, creating a uniform, matte finish.
Tumbling
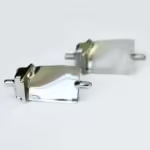
Electropolish
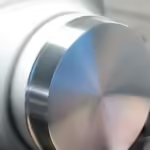
Electropolish is a chemical process that smooths and brightens surfaces while improving corrosion resistance.
Alodine
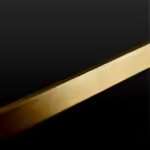
Alodine coating provides corrosion protection and improves paint adhesion, mainly used on aluminum surfaces.
Heat Treatment
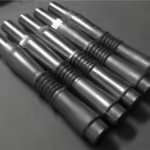
Brushed Finish
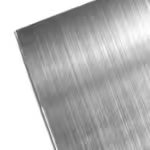
A brushed finish creates a unidirectional satin texture, reducing the visibility of marks and scratches on the surface.
Powder Coating
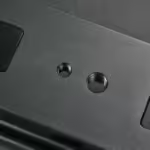
Powder coating applies a thick, wear-resistant layer with excellent color and texture options, suitable for a variety of surfaces.
Electroplating
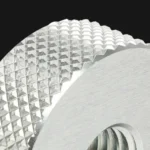
Electroplating bonds a thin metal layer onto parts, improving wear resistance, corrosion resistance, and surface conductivity.
Black Oxidize
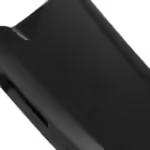
Tolerances for CNC Turning
As an ISO 9001 certified company, we manufacture CNC turning lathe parts to meet stringent tolerance requirements. Depending on your design, our CNC lathes can achieve tolerances of up to ±0.005”. Our standard tolerances for CNC milled metals comply with ISO 2768-m, while for plastics, we adhere to ISO 2768-c.
Description | |
Maximum Part Size | Typically up to 500 mm in diameter and 1500 mm in length, though larger sizes can be accommodated with specific equipment. |
Minimum Part Size | As small as 1 mm in diameter, depending on the material and machining setup. |
General Tolerances | Standard tolerances of ±0.01 mm; tighter tolerances down to ±0.005 mm can be achieved based on the material and complexity of the part. |
Lead Time | Standard lead times range from 3-7 days for small batches. Expedited services are available, reducing lead time to 24-48 hours depending on part complexity and material availability. |
CNC Turning Design Guidelines
Recommended Size | |
Radii | Minimum internal radius of 0.5 mm recommended. Larger radii (up to 3 mm or more) can improve tool access and reduce stress concentrations in the part. |
Threads and Tapped Holes | External and internal threads can be precisely cut. Standard thread sizes from M1.6 and larger are feasible. Ensure a minimum thread length of 1.5 times the diameter for stability. |
Minumum Wall Thickness | Maintain a minimum wall thickness of 0.8 mm for metals and 1.5 mm for plastics to ensure structural integrity without compromising the machining process. |
Text | Engraving should have a minimum character height of 2 mm and a depth of at least 0.5 mm to ensure legibility after machining. |
Holes | Minimum hole diameter of 0.5 mm. For deep holes, maintain a diameter to depth ratio of 1:10 to avoid tool deflection and ensure hole quality. |
How Does CNC Turning Work?
CNC turning is a subtractive manufacturing process that utilizes computer-controlled lathes to accurately shape materials into cylindrical parts. The design is first created using CAD software, then converted into instructions for the CNC machine through CAM software. During setup, the appropriate cutting tools are installed, and a cylindrical workpiece is secured in the machine’s chuck, which holds and rotates the material.
As the machine operates, the workpiece spins at high speeds while cutting tools move along various axes to carve and shape the material according to the program’s specifications. Operations such as facing, threading, knurling, and drilling occur during this phase, often with coolant applied to prevent overheating and clear debris.
Following machining, the part may go through additional finishing processes like sanding or polishing. The final step is a thorough inspection to ensure it meets all required dimensions and tolerances. This method provides high precision and repeatability, making CNC turning ideal for efficiently producing complex parts.
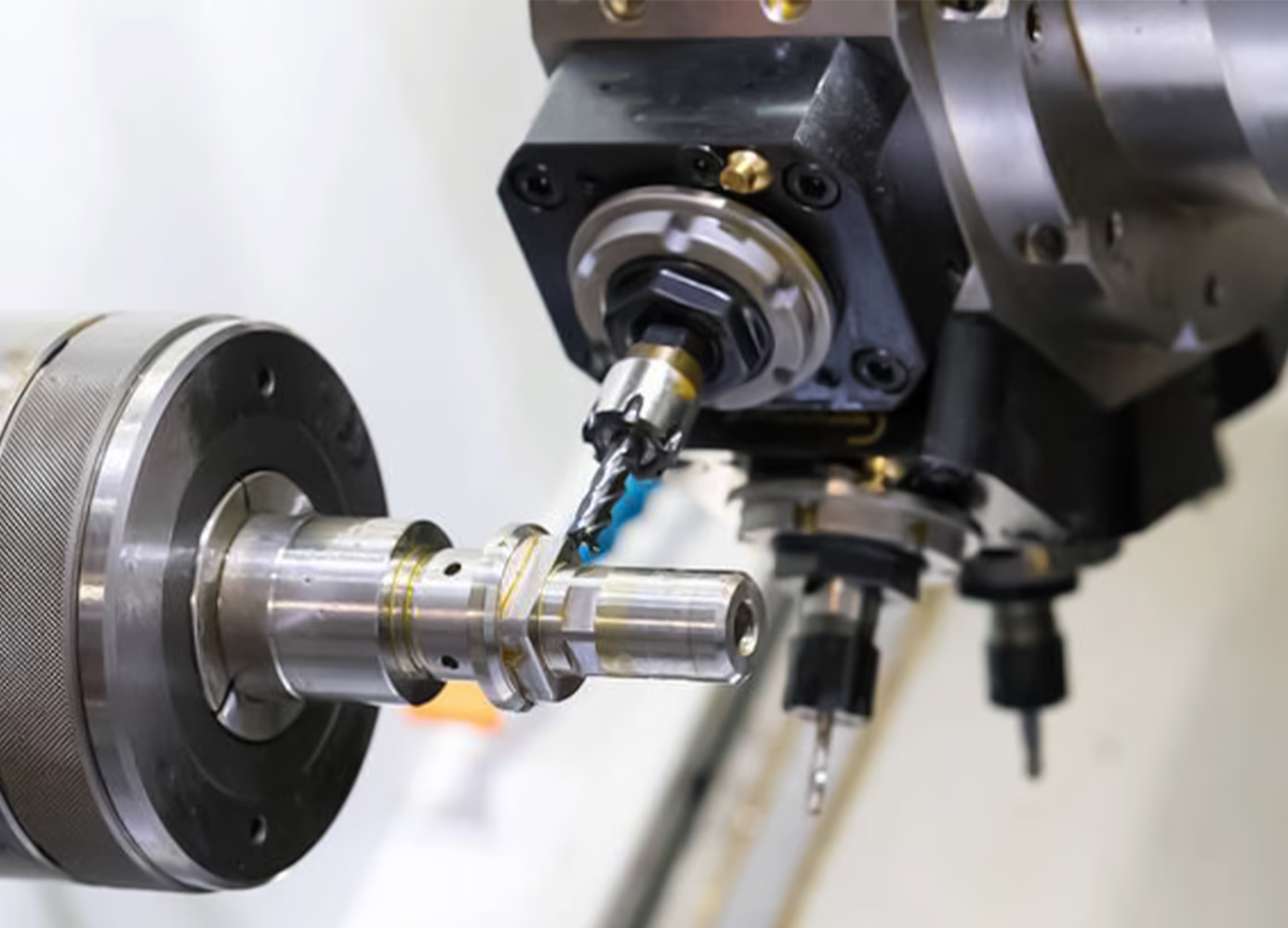
Advantages
Advantages of CNC Turning
CNC turning offers several key advantages that make it a preferred method for manufacturing precise cylindrical parts. Here are some of the main benefits:
- Precision and Accuracy: Machines are capable of achieving extremely tight tolerances, essential for components that must fit seamlessly into complex assemblies.
- Efficiency: Once programmed and set up, these machines produce parts quickly and with consistent quality, often requiring minimal supervision, which accelerates production cycles.
- Flexibility: The ability to reprogram the machines for different designs quickly makes them highly adaptable to varying production needs, enhancing operational responsiveness.
- Repeatable: The automated nature ensures that each part is identical, even across large production volumes, crucial for maintaining quality in mass production.
- Reduced Labor Costs: Automation reduces the need for manual intervention, cutting labor costs and minimizing human error, thereby enhancing overall efficiency and cost-effectiveness.
- Material Versatility: The machines handle a wide range of materials, from various metals to plastics and composites, accommodating diverse manufacturing demands.
- Improved Safety: The enclosed, automated operation minimizes human interaction, reducing the risk of accidents and promoting a safer workplace.
Applications
Applications of CNC Turning
- Shafts are fundamental in various machines, serving as axes or pivots. Precision in diameter and surface finish is crucial for their interaction with other mechanical parts.
- Flanges connect pipes, pumps, or valves, requiring accurate machining to ensure a secure fit and avoid leaks.
- Bushings and Sleeves provide smooth surfaces for other parts to move against or through, necessitating exact internal diameters and smooth finishes.
- Pins are small but vital for aligning or holding components together, often needing precise dimensions to fit snugly into place.
- Knobs and Dials are user interface elements for machinery and electronic devices, where aesthetics and precise dimensions enhance usability.
- Wheels and Rollers are integral to systems like conveyors, where consistent shape and smoothness reduce friction and wear.
CNC Turning FAQs
Technical FAQs
What minimum thickness can I incorporate into my design to prevent warpage?
What size of fillets are added when no specific fillet is specified by the 3D model or drawing?
If a specific fillet radius is required, please specify. If not, the fillet radii that allow for easy machining will be added based on the machinist’s discretion. For a general idea, internal vertical edge radii could be >1/3*Depth and internal horizontal edges may be left sharp or have a 0.5mm to 1mm radius.
General FAQs
What is the difference between rough turning and finish turning?
Rough turning removes as much material as possible without a focus on accuracy and surface finish, getting the workpiece close to the desired shape. Finish turning “finishes” the process, producing the desired smoothness and accuracy.
What is the difference between CNC turning centers and CNC lathes?
What are the benefits of CNC turning?
In addition to using turning tools, a CNC turning center can also be equipped with rotating cutters such as end mills or drills, which allows for greater freedom in machining, such as having the ability to handle asymmetrical features in parts. This increases production speed and efficiency, cost-effectiveness and safer operations. Several aspects of turning that are unique and different from milling, include the ease of achieving radial symmetry, high precision due to mounting part in chuck, and good surface finish.
What parts can be made with CNC turning?
CNC turning is used for creating a variety of parts, including auto parts, knobs, tubes, gears, toy parts, flywheels, crankshafts, hubs & disc cams. It is most often used to manufacture parts for automotive, aerospace, medical, and other industries.
Let's Start A New Project Today